Engine high-voltage wire press-fitting device
A high-voltage wire and press-fitting device technology, which is applied in metal processing, metal processing equipment, manufacturing tools, etc., can solve the problem of uncontrollable contact between the rubber hammer and the high-voltage wire head, affecting the internal quality of the high-voltage wire, and local stress on the high-voltage wire head major issues
- Summary
- Abstract
- Description
- Claims
- Application Information
AI Technical Summary
Problems solved by technology
Method used
Image
Examples
Embodiment 1
[0032] Embodiment 1: A kind of press-fitting device for engine high-voltage wires (see attached figure 1 attached figure 2 ), including a door-shaped bracket fixed on the ground, a slide rail 5 is connected to the upper end of the bracket, and a pressure rod 1 is hinged on the slide rail.
[0033] The support includes two uprights 8 and an upper pole 6 horizontally fixed on the upper end of the upright, the height of the upper pole relative to the upright can be adjusted, and the two ends of the upper pole are fixed with stoppers 7 made of polyurethane material. Horizontally be fixed with track 16 on the last bar, and track is in the side position of last bar. The upper surface of the track has a raised anti-off strip 17 (see attached Figure 7 ), the cross-section of the anti-off strip is triangular, the slide rail has a transverse buckle groove, the buckle groove buckles the track, and the upper surface of the buckle groove is provided with an anti-off groove 18 matching ...
Embodiment 2
[0036] Embodiment 2: A kind of press-fitting device for engine high-voltage wires (see attached Figure 8 ), the difference from Embodiment 1 is that the pressure head includes a jacket 19 matched with the high-voltage wire head and a pressing head arranged in the jacket, and an oil chamber 20 is arranged in the jacket, and the oil chamber is closed by a sealing plate 21, and the sealing The board is provided with several evenly distributed through holes 23 (see attached Figure 9 ). The pressing head includes pressing rods 22 whose number is equal to the number of through holes and a movable plate 23 hinged at the end of the pressing rods. The surfaces of all the movable plates form the pressing surface, which is adapted to the shape of the end face of the high-voltage wire head and forms a Full contact, the pressing rod extends through the through hole into the oil chamber to form a piston structure, and the tail end of the oil chamber is equipped with an oil injection devi...
Embodiment 3
[0038] Embodiment 3: A kind of press-fitting device for engine high-voltage wires (see attached Figure 10 ), the difference with Embodiment 2 is that: an oil chamber is arranged in the jacket, and the pressing head is a flexible membrane 25 fixed in the jacket, and the flexible membrane seals the oil chamber, and the area of the flexible membrane is the same as the area of the end surface of the high-voltage wire head. Adapting, the pressing surface is the surface of the flexible membrane facing outwards, the pressing surface changes with the shape of the end surface of the high-voltage wire head and forms full contact. Refer to Example 2 for the rest of the structures.
PUM
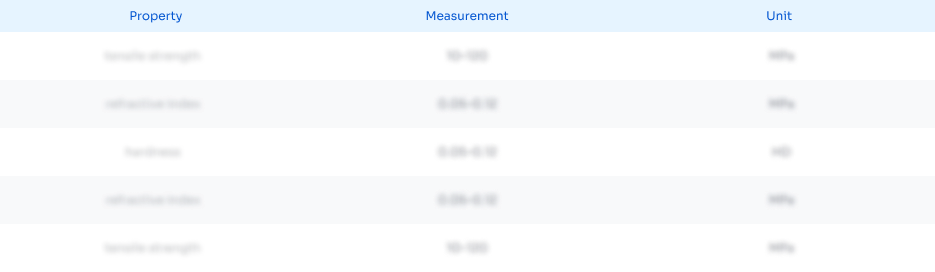
Abstract
Description
Claims
Application Information

- R&D
- Intellectual Property
- Life Sciences
- Materials
- Tech Scout
- Unparalleled Data Quality
- Higher Quality Content
- 60% Fewer Hallucinations
Browse by: Latest US Patents, China's latest patents, Technical Efficacy Thesaurus, Application Domain, Technology Topic, Popular Technical Reports.
© 2025 PatSnap. All rights reserved.Legal|Privacy policy|Modern Slavery Act Transparency Statement|Sitemap|About US| Contact US: help@patsnap.com