Manufacturing method of optical fiber F-P cavity sensor and manufacturing device thereof
A production device, F-P technology, applied in the direction of optical device transmission of sensing components, optical waveguide coupling, etc., can solve the problems of poor sealing performance, inability to withstand high temperature strength, and inapplicability, and achieve uniform angular stress and sealing performance Good, guarantee the effect of reliability
- Summary
- Abstract
- Description
- Claims
- Application Information
AI Technical Summary
Problems solved by technology
Method used
Image
Examples
Embodiment 1
[0032] Such as Figure 1-2 As shown, a manufacturing device of an optical fiber F-P cavity sensor, it includes a device bracket 1 provided with a fixing seat 5, in which a tapered roller bearing 4 is fixed; the top of the hollow fixed shaft 3 and the hollow three-claw clamp The disk 2 is fixedly connected; the middle part of the fixed shaft 3 passes through the tapered roller bearing 4 and is supported and fixed on the device bracket 1 and pivots around the axis of the fixed shaft 3 relative to the device bracket 1. The bottom of the fixed shaft 3 is fixedly connected with the large synchronous pulley 6 ;; The small synchronous pulley 7 driven by the large synchronous pulley 6 and the stepper motor 8 is driven by a belt; the hollow tube shaft 18 passes through the center of the three-jaw chuck 2 and the fixed shaft 3, and the upper part of the tube shaft 18 is clamped by the three-jaw The disc 2 is clamped and rotated with the three-jaw chuck 2. The lower end of the tube shaft...
Embodiment 2
[0035] The similarities between this embodiment and Embodiment 1 will not be repeated, and the difference is that it is a method for manufacturing an optical fiber F-P cavity sensor, which uses the manufacturing device for an optical fiber F-P cavity sensor described in Embodiment 1, which includes the following step:
[0036] (1) Set up the welding system device, fix the tapered roller bearing 4 in the fixed seat 5, extend the fixed shaft 3 into the three-jaw chuck 2 and the tapered roller bearing 4 and fix it, and use the fastening nut 12 to secure the large synchronous The pulley 6 is fixed in position, and the small synchronous pulley 7 and the stepping motor 8 are connected, and the tube shaft 18 is inserted into the gap between the three-jaw chuck 2, the fixed shaft 3 and the tapered roller bearing 4, and inserted into the base of the tube shaft In 19, the tube shaft 18 and the tube shaft base 19 realize dynamic sealing through the sealing ring 23, and the tube shaft bas...
PUM
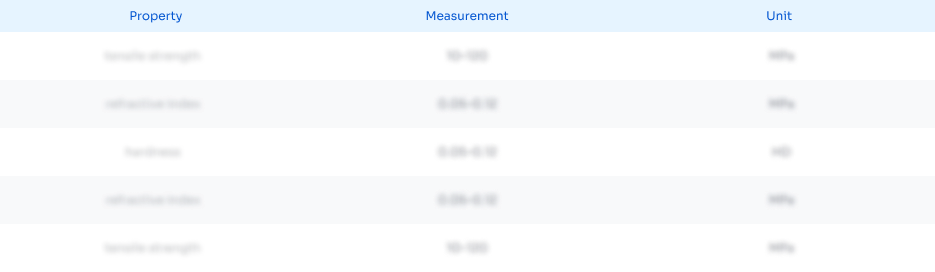
Abstract
Description
Claims
Application Information

- R&D
- Intellectual Property
- Life Sciences
- Materials
- Tech Scout
- Unparalleled Data Quality
- Higher Quality Content
- 60% Fewer Hallucinations
Browse by: Latest US Patents, China's latest patents, Technical Efficacy Thesaurus, Application Domain, Technology Topic, Popular Technical Reports.
© 2025 PatSnap. All rights reserved.Legal|Privacy policy|Modern Slavery Act Transparency Statement|Sitemap|About US| Contact US: help@patsnap.com