Method for welding large special-shaped multicavity steel structure
A welding method and multi-cavity technology, applied in welding equipment, metal processing equipment, manufacturing tools, etc., can solve the problem that special-shaped multi-cavity giant steel structures cannot be welded with ordinary box steel structures, and reduce the repair rate of weld seams. , The effect of reducing the amount of welding works, reducing deformation and residual stress
- Summary
- Abstract
- Description
- Claims
- Application Information
AI Technical Summary
Problems solved by technology
Method used
Image
Examples
Embodiment Construction
[0028] The following clearly and completely describes the technical solutions in the embodiments of the present invention. Obviously, the described embodiments are only some of the embodiments of the present invention, but not all of them. Based on the embodiments of the present invention, all other embodiments obtained by persons of ordinary skill in the art without making creative efforts belong to the protection scope of the present invention.
[0029] An embodiment of the present invention provides a welding method for a special-shaped multi-cavity giant steel structure, such as figure 1 As shown, the method includes:
[0030] Obtain the size of the special-shaped multi-cavity giant steel structure, and segment the special-shaped multi-cavity giant steel structure into multi-section assembly units according to the size;
[0031] Determine the welding sequence according to the structure of each assembled unit after segmentation;
[0032] Weld the assembled units of each s...
PUM
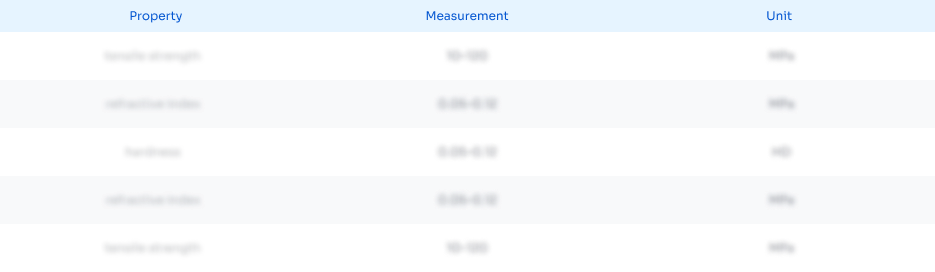
Abstract
Description
Claims
Application Information

- R&D
- Intellectual Property
- Life Sciences
- Materials
- Tech Scout
- Unparalleled Data Quality
- Higher Quality Content
- 60% Fewer Hallucinations
Browse by: Latest US Patents, China's latest patents, Technical Efficacy Thesaurus, Application Domain, Technology Topic, Popular Technical Reports.
© 2025 PatSnap. All rights reserved.Legal|Privacy policy|Modern Slavery Act Transparency Statement|Sitemap|About US| Contact US: help@patsnap.com