Oil cylinder core tube cavitation corrosion prevention system for crane and crane with same
A crane and oil cylinder technology, applied in the field of cranes, can solve problems such as delay, loss of user economic benefits, vehicle damage, etc., and achieve the effects of avoiding extension delay phenomenon, avoiding pipeline vibration failure, and avoiding core tube cavity cavitation problems.
- Summary
- Abstract
- Description
- Claims
- Application Information
AI Technical Summary
Problems solved by technology
Method used
Image
Examples
Embodiment 1
[0023] like figure 1 As shown, a system for preventing cavitation of cylinder core tubes for cranes, the system includes a telescopic switching valve (not shown in the figure), an anti-cavitation overflow valve 1, a first directional control valve 2, and a second directional control valve 8 1. The first-stage oil cylinder 5 and the second-stage oil cylinder 7. The telescopic switching valve includes a pressure oil port P and an oil return port T. The pressure oil port P is connected to the system pressure oil circuit, and the oil return port T is connected to the system oil return circuit; The anti-cavitation overflow valve 1 includes a first oil port 11 and a second oil port 12, the first oil port 11 communicates with the oil return port T of the telescopic switching valve; the first directional control valve 2 includes a first control oil port 25. The second control oil port 26, four working oil ports and two working positions, the first working oil port 23 communicates with...
Embodiment 2
[0038] like figure 2 As shown in the figure, a system for preventing cavitation of the core tube of a cylinder for a crane includes a telescopic switching valve (not shown in the figure), a direct-acting overflow valve 10, a one-way valve 9, a first directional control valve 2, a second The two-way control valve 8, the first-stage oil cylinder 5 and the second-stage oil cylinder 7, the telescopic switching valve includes a pressure oil port P and an oil return port T, the pressure oil port P is connected with the system pressure oil circuit, and the oil return port T is connected with the system return port The oil circuit is connected; the direct-acting relief valve 10 and the one-way valve 9 are arranged in parallel, the direct-acting relief valve 10 includes an inlet 102 and an outlet 101, the one-way valve 9 includes an inlet 91 and an outlet 92, and the direct-acting overflow The outlet 101 of the valve 10 and the inlet 91 of the one-way valve 9 communicate with the oil ...
PUM
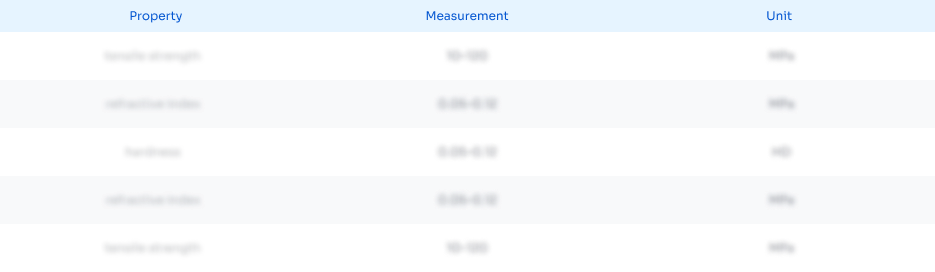
Abstract
Description
Claims
Application Information

- R&D
- Intellectual Property
- Life Sciences
- Materials
- Tech Scout
- Unparalleled Data Quality
- Higher Quality Content
- 60% Fewer Hallucinations
Browse by: Latest US Patents, China's latest patents, Technical Efficacy Thesaurus, Application Domain, Technology Topic, Popular Technical Reports.
© 2025 PatSnap. All rights reserved.Legal|Privacy policy|Modern Slavery Act Transparency Statement|Sitemap|About US| Contact US: help@patsnap.com