Method for reducing steam temperature deviation by using steam soot blowing for boiler of thermal power plant
A technology for thermal power plants and steam temperature deviation, which is applied in the field of steam soot blowing to reduce steam temperature deviation, can solve the problems of increasing the power of medium and low pressure cylinders, uneven smoke velocity, actual tangent circle and reduction of residual torque of airflow, etc. The effect of alternating stress, the effect of improving equipment safety and reducing the probability of blowing damage
- Summary
- Abstract
- Description
- Claims
- Application Information
AI Technical Summary
Problems solved by technology
Method used
Examples
Embodiment Construction
[0025] The invention provides a method for adjusting steam temperature deviation by steam soot blowing for a boiler in a thermal power plant, which specifically includes the following steps:
[0026] Step 1, under the condition of normal combustion in the boiler furnace, introduce steam into the soot blower,
[0027] Step 2, use the steam in the soot blower to heat different areas of the superheater (including the primary, secondary, and tertiary levels) and reheater (including the primary, secondary, etc.) of the boiler, Differential soot blowing is carried out according to the temperature distribution of the heating surface of the part, so as to change the surface soot accumulation degree of different areas and parts of the superheater and reheater;
[0028] Step 2 includes step 3, judging the outlet steam temperature deviation of a certain stage of the superheater and reheater (for example, it can be divided into A and B sides, or it can be divided into A, B, C sides, or ev...
PUM
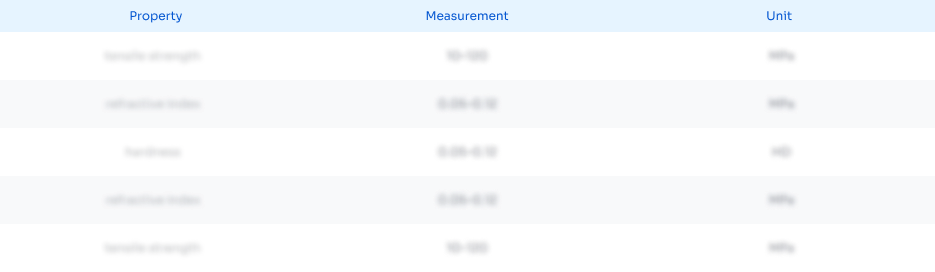
Abstract
Description
Claims
Application Information

- R&D Engineer
- R&D Manager
- IP Professional
- Industry Leading Data Capabilities
- Powerful AI technology
- Patent DNA Extraction
Browse by: Latest US Patents, China's latest patents, Technical Efficacy Thesaurus, Application Domain, Technology Topic, Popular Technical Reports.
© 2024 PatSnap. All rights reserved.Legal|Privacy policy|Modern Slavery Act Transparency Statement|Sitemap|About US| Contact US: help@patsnap.com