Method of preparing calcium gluconate by composite immobilized enzyme
A technology of calcium gluconate and immobilized enzymes, applied in the direction of immobilization on or in inorganic carriers, on/in organic carriers, chemical industry, etc., can solve the problem of low enzyme immobilization rate and recovery rate, low price, etc. High cost and other issues, to achieve the effect of low price, increased reuse times, and improved reuse rate
- Summary
- Abstract
- Description
- Claims
- Application Information
AI Technical Summary
Problems solved by technology
Method used
Image
Examples
Embodiment 1
[0031] (1) Prepare 1500mL sodium alginate and silica gel mixed solution, the concentration of sodium alginate is 1.0%-1.5%, the concentration of silica gel is 1.0%-2.0% (calculated as sodium silicate), sterilize at 121°C and cool it down. Glucose oxidase equivalent to 2.5‰ of the glucose quality in the reaction solution and 7.5‰ of catalase were added to it, and fully stirred evenly; using a syringe, mix sodium alginate and silica gel mixed with glucose oxidase and catalase Drop the mixed solution solution into the 6% calcium chloride solution that has been sterilized and cooled to fix the shape, and let it stand still for 4 hours; use anhydrous glucose to prepare 3.5L glucose solution with a concentration of 10% (W / V), put it in the In the 5L reaction tank, first add 32.4g of calcium carbonate solid; add the formed immobilized enzyme into the reaction tank, and set the reaction conditions as follows: sterile air is introduced, the stirring speed is 200-300 r / min, and the enzym...
Embodiment 2
[0035](1) Prepare 16L mixed solution of sodium alginate and silica gel, the concentration of sodium alginate is 1.0%-1.5%, the concentration of silica gel is 1.0%-2.0% (calculated as sodium silicate), sterilize at 121°C and cool down. Glucose oxidase and 1% catalase, which is equivalent to 2.5‰ of the glucose mass in the reaction solution, were added to it, and fully stirred evenly; using a peristaltic pump with multiple syringe needles, mixed glucose oxidase and catalase Drop the mixed solution of sodium alginate and silica gel into the sterilized and cooled 5% calcium chloride solution to fix the shape, and let it stand still for 6 hours; use anhydrous glucose to prepare 70L glucose solution with a concentration of 10% (W / V), and disinfect After cooling, put it in a 100L reaction tank, first add 640g of calcium carbonate solid; add the formed immobilized enzyme into the reaction tank, set the reaction conditions as follows: feed sterile air, stirring speed 200-300 r / min, enzy...
Embodiment 3
[0038] A comparative example is as follows:
[0039] Using anhydrous glucose, prepare 70L of glucose solution with a concentration of 10% (W / V), put it in a 100L reaction tank after disinfection and cooling, add glucose oxidase and peroxidase, and add 640g of calcium carbonate solid first; set the reaction conditions as : Sterile air was introduced, the stirring speed was 200-300 r / min, and the enzyme reaction temperature was 33°C; after 6 hours of reaction, add the remaining 1300g of calcium carbonate solid (slightly excessive calcium carbonate), and continue the reaction for 20 hours, and the reaction liquid After the reducing sugar concentration drops below 0.2%, stop the reaction, stop ventilation, stir, take out the reaction solution, add activated carbon at 0.7% (W:V) to decolorize at 75 ° C for 1 hour, filter to obtain the filtrate, and the vacuum degree is 0.095MPa Under the conditions, evaporate at 60°C until the dry matter percentage is 70%, add 1% calcium gluconate ...
PUM
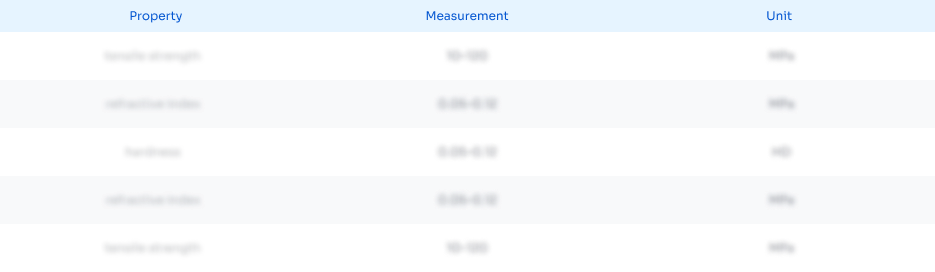
Abstract
Description
Claims
Application Information

- R&D
- Intellectual Property
- Life Sciences
- Materials
- Tech Scout
- Unparalleled Data Quality
- Higher Quality Content
- 60% Fewer Hallucinations
Browse by: Latest US Patents, China's latest patents, Technical Efficacy Thesaurus, Application Domain, Technology Topic, Popular Technical Reports.
© 2025 PatSnap. All rights reserved.Legal|Privacy policy|Modern Slavery Act Transparency Statement|Sitemap|About US| Contact US: help@patsnap.com