Device and method for manufacturing mould of mini-sized impeller with high height-thickness ratio
A miniature, impeller technology, applied in the direction of manufacturing tools, forging/pressing/hammer devices, forging/pressing/hammering machinery, etc., can solve the problems of unsuitable batch manufacturing, less machinable materials, and low processing efficiency, and achieve good results Comprehensive mechanical properties, improved surface quality, and convenient die replacement
- Summary
- Abstract
- Description
- Claims
- Application Information
AI Technical Summary
Problems solved by technology
Method used
Image
Examples
specific Embodiment approach 1
[0025] Specific implementation mode one: combine figure 1 and figure 2 Describe this embodiment, this embodiment includes upper mold base 1, lower mold base 2, punch fixing plate 3, punch 4, die fixing plate 5, die backing plate 6, insert type die 7, ejector pin 8. Heating ring 9, ejection screw 12, multiple guide sleeves 10 and multiple guide pillars 11, the upper mold base 1 and the lower mold base 2 are arranged in parallel up and down, and multiple guide sleeves are arranged around the upper mold base 1 10. One end of each guide post 11 is set on the bottom end surface of the lower mold base 2, the other end of each guide post 11 can be slidably set in a guide sleeve 10, and the punch 4 is set on the punch fixing plate 3 On the top, the punch fixing plate 3 is fixed on the bottom end surface of the upper die base 1, the die fixing plate 5 is fixed on the lower die base 2, the die fixing plate 5 is provided with a die placement hole 5-1, the die The backing plate 6 is se...
specific Embodiment approach 2
[0033] Specific implementation mode two: combination figure 1 The present embodiment will be described. The punch fixing plate 3 of the present embodiment is fixed to the bottom end surface of the upper die base 1 by fastening screws. With such a setting, the connection is convenient. Other compositions and connections are the same as in the first embodiment.
specific Embodiment approach 3
[0034] Specific implementation mode three: combination figure 1 The present embodiment will be described. The die fixing plate 5 of the present embodiment is fixed to the lower die base 2 with fastening screws. With such a setting, the connection is convenient. Other compositions and connections are the same as those in the second embodiment.
PUM
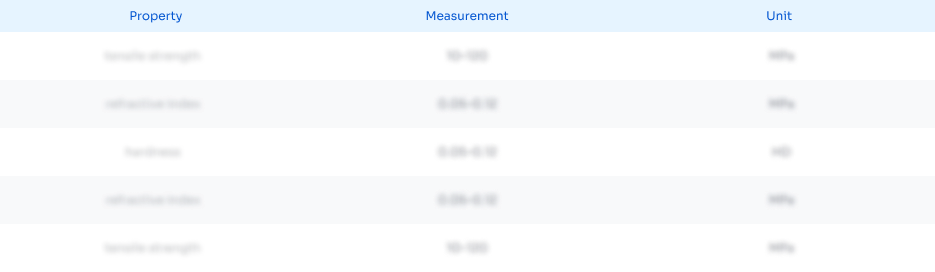
Abstract
Description
Claims
Application Information

- R&D
- Intellectual Property
- Life Sciences
- Materials
- Tech Scout
- Unparalleled Data Quality
- Higher Quality Content
- 60% Fewer Hallucinations
Browse by: Latest US Patents, China's latest patents, Technical Efficacy Thesaurus, Application Domain, Technology Topic, Popular Technical Reports.
© 2025 PatSnap. All rights reserved.Legal|Privacy policy|Modern Slavery Act Transparency Statement|Sitemap|About US| Contact US: help@patsnap.com