PID (Proportion Integration Differentiation) controller optimizing design method based on particle swarm membrane algorithm
An optimization design and controller technology, applied in the direction of adaptive control, general control system, control/regulation system, etc., can solve problems such as long adjustment time, failure to obtain the global optimal value, and failure of the controlled system to obtain satisfactory control effects, etc.
- Summary
- Abstract
- Description
- Claims
- Application Information
AI Technical Summary
Problems solved by technology
Method used
Image
Examples
Embodiment
[0074] Using the present invention to optimize the design of PID controllers for four classic single-input single-output (SISO) controlled objects, the mathematical models of the four objects are shown in the following formulas (3) to (6), which are first-order inertia plus pure Hysteresis link (model of most chemical processes), second-order inertia plus pure lag link (large lag time constant), third-order linear system and fourth-order linear system with non-minimum phase, where G 1 (s), G 2 (s), G 3 (s) and G 4 (s) represent functions of objects I, II, III and IV in the complex frequency domain (s domain), respectively. The performance index adopted in the embodiment comprises single item performance index overshoot (T s ), adjustment time (σ) and integral absolute error performance index (IAE), using Matlab7.5 as the implementation tool, and solving on a computer with Windows XP operating system, AMD Sempron 1.6GHz CPU and 1GB memory.
[0075] Object I:
[0076] ...
PUM
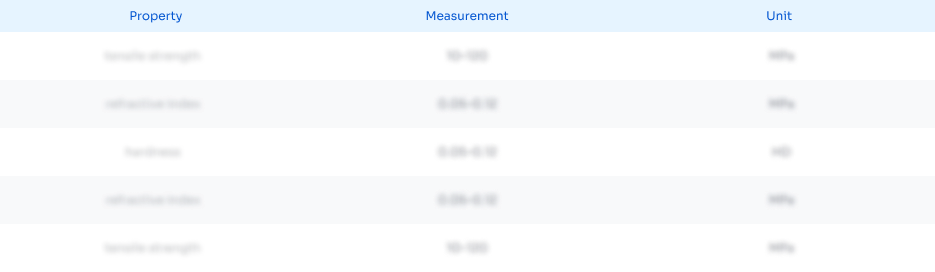
Abstract
Description
Claims
Application Information

- R&D
- Intellectual Property
- Life Sciences
- Materials
- Tech Scout
- Unparalleled Data Quality
- Higher Quality Content
- 60% Fewer Hallucinations
Browse by: Latest US Patents, China's latest patents, Technical Efficacy Thesaurus, Application Domain, Technology Topic, Popular Technical Reports.
© 2025 PatSnap. All rights reserved.Legal|Privacy policy|Modern Slavery Act Transparency Statement|Sitemap|About US| Contact US: help@patsnap.com