Method for preparing modified lignosulfonate water reducing agent with acrylic waste water as raw material
A technology of lignosulfonate and acrylic acid, applied in the field of building materials, can solve the problems of low energy consumption, low treatment rate, and secondary pollution of biological methods
- Summary
- Abstract
- Description
- Claims
- Application Information
AI Technical Summary
Problems solved by technology
Method used
Image
Examples
Embodiment 1
[0026] The content of acrylic acid, sodium hypophosphite (reducing agent), and methanesulfonic acid (catalyst) in the acrylic acid waste liquid were determined to be 4.2%, 2.5%, and 2.4% respectively. Sodium lignosulfonate was used, and the reducing agent content in the index was 7.2%. .
[0027] Put 100 parts of lignosulfonate and 250 parts of deionized water in a synthetic reaction vessel, mix well, heat to 80°C, and stabilize at 80±2°C, add 10 parts of permanganic acid after stabilization; add 6 parts of persulfuric acid Ammonium and 206 parts of deionized water were mixed evenly and placed in the dripping container B. After the temperature of the permanganic acid solution added to the synthesis reaction container was stabilized for 5 minutes, the liquid in the container B was started to be added dropwise, and the dripping was completed in 4.5 hours; 320 parts of acrylic acid waste liquid (with 10 parts of permanganic acid added) and 11 parts of sodium methacrylate were mix...
Embodiment 2
[0029] The content of acrylic acid, sodium nitrite (reducing agent) and p-toluenesulfonic acid (catalyst) in the butyl acrylate waste liquid was determined to be 5.8%, 1.8%, and 2.8% respectively. Calcium lignosulfonate was used, and the content of reducing agent in the index 9.0%.
[0030] Put 100 parts of calcium lignosulfonate and 250 parts of deionized water in a synthetic reaction vessel, mix well, heat to 60°C, and stabilize at 60±2°C, add 10 parts of permanganic acid after stabilization; add 6 parts of persulfuric acid Ammonium and 206 parts of deionized water were mixed evenly and placed in the dripping container B. After the temperature of the permanganic acid solution added to the synthesis reaction container was stabilized for 5 minutes, the liquid in the container B was started to be added dropwise, and the dripping was completed in 4.5 hours; 320 parts of acrylic acid waste liquid (with 11 parts of permanganic acid added) and 12.5 parts of sodium methacrylate were...
Embodiment 3
[0032] The content of acrylic acid, sodium nitrite (reducing agent) and p-toluenesulfonic acid (catalyst) in the butyl acrylate waste liquid was determined to be 5.8%, 1.8%, and 2.8% respectively. Calcium lignosulfonate was used, and the content of reducing agent in the index 9.0%.
[0033] Put 100 parts of lignosulfonate and 250 parts of deionized water in a synthetic reaction vessel, mix well, heat to 80°C, and stabilize at 80±2°C, add 10 parts of permanganic acid after stabilization; add 6 parts of persulfuric acid Ammonium and 206 parts of deionized water were mixed evenly and placed in the dripping container B. After the temperature of the permanganic acid solution added to the synthesis reaction container was stabilized for 5 minutes, the liquid in the container B was started to be added dropwise, and the dripping was completed in 4.5 hours; 112 parts of acrylic acid waste liquid (with 10 parts of permanganic acid added) and 15 parts of sodium methacrylate were mixed eve...
PUM
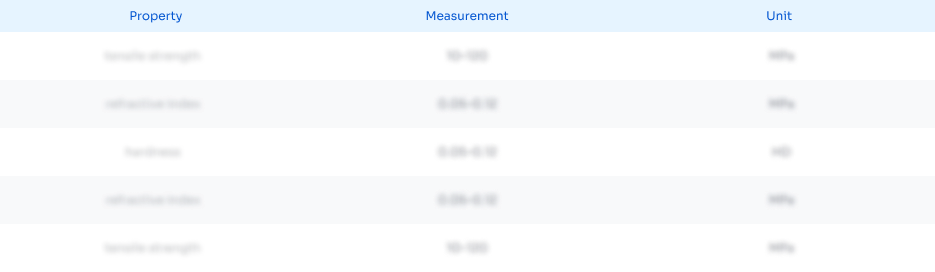
Abstract
Description
Claims
Application Information

- R&D
- Intellectual Property
- Life Sciences
- Materials
- Tech Scout
- Unparalleled Data Quality
- Higher Quality Content
- 60% Fewer Hallucinations
Browse by: Latest US Patents, China's latest patents, Technical Efficacy Thesaurus, Application Domain, Technology Topic, Popular Technical Reports.
© 2025 PatSnap. All rights reserved.Legal|Privacy policy|Modern Slavery Act Transparency Statement|Sitemap|About US| Contact US: help@patsnap.com