Method for preventing machining deformation of thin-walled work-piece
A thin-walled part processing and to-be-processed technology, applied in the thin-walled part processing technology field, can solve problems such as processing deformation, and achieve the effect of preventing processing deformation and workpiece deformation
- Summary
- Abstract
- Description
- Claims
- Application Information
AI Technical Summary
Problems solved by technology
Method used
Image
Examples
Embodiment 1
[0015] This embodiment provides a method for preventing processing deformation of thin-walled parts, which is characterized in that: the method for preventing processing deformation of thin-walled parts involves an outer circle with a size of 150-3000mm. For wall parts, it is required that the clamping method of the parts during processing is compression, and there are mounting edges at both ends of the processed parts. After processing to the required size, the process mounting edges are removed, and the parts are installed on the faceplate or chuck of the machine tool for compression. Align the point, rough machine the upper end surface and the outer circle or cone surface, turn around and align with the processed end surface and the outer circle of the installation edge, press the lower end surface, measure the deformation error of the processed end surface with a feeler gauge; then use the equal error After inserting the spacer or feeler gauge with the same value into the c...
Embodiment 2
[0019] This embodiment provides a method for preventing processing deformation of thin-walled parts, which is characterized in that: the method for preventing processing deformation of thin-walled parts involves an outer circle with a size of 150-3000mm. For wall parts, it is required that the clamping method of the parts during processing is compression, and there are mounting edges at both ends of the processed parts. After processing to the required size, the process mounting edges are removed, and the parts are installed on the faceplate or chuck of the machine tool for compression. Align the point, rough machine the upper end surface and the outer circle or cone surface, turn around and align with the processed end surface and the outer circle of the installation edge, press the lower end surface, measure the deformation error of the processed end surface with a feeler gauge; then use the equal error After inserting the spacer or feeler gauge with the same value into the c...
Embodiment 3
[0023] This embodiment provides a method for preventing processing deformation of thin-walled parts, which is characterized in that: the method for preventing processing deformation of thin-walled parts involves an outer circle with a size of 150-3000mm. For wall parts, it is required that the clamping method of the parts during processing is compression, and there are mounting edges at both ends of the processed parts. After processing to the required size, the process mounting edges are removed, and the parts are installed on the faceplate or chuck of the machine tool for compression. Align the point, rough machine the upper end surface and the outer circle or cone surface, turn around and align with the processed end surface and the outer circle of the installation edge, press the lower end surface, measure the deformation error of the processed end surface with a feeler gauge; then use the equal error After inserting the spacer or feeler gauge with the same value into the c...
PUM
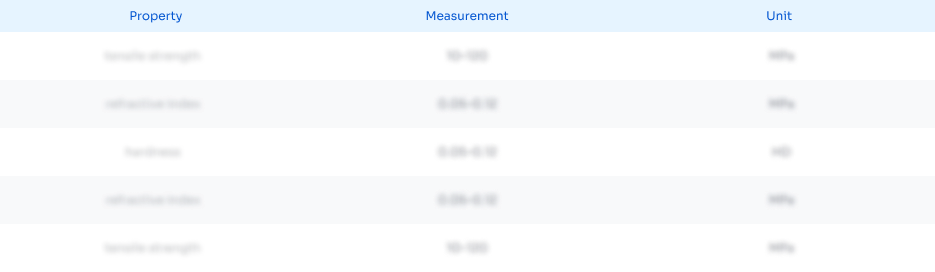
Abstract
Description
Claims
Application Information

- R&D Engineer
- R&D Manager
- IP Professional
- Industry Leading Data Capabilities
- Powerful AI technology
- Patent DNA Extraction
Browse by: Latest US Patents, China's latest patents, Technical Efficacy Thesaurus, Application Domain, Technology Topic, Popular Technical Reports.
© 2024 PatSnap. All rights reserved.Legal|Privacy policy|Modern Slavery Act Transparency Statement|Sitemap|About US| Contact US: help@patsnap.com