Rolling schedule comprehensive optimization method for cold continuous rolling unit taking scratch prevention as objective
A technology of cold tandem rolling unit and rolling schedule, which is applied in metal rolling, metal rolling, manufacturing tools, etc., and can solve the problems of inaccurate comprehensive judgment index forecasting and other problems
- Summary
- Abstract
- Description
- Claims
- Application Information
AI Technical Summary
Problems solved by technology
Method used
Image
Examples
Embodiment 1
[0048] A method for comprehensive optimization of rolling schedules with the goal of preventing and controlling roughening in a tandem cold rolling mill. The steps are as follows: figure 1 Shown:
[0049] First, in step 1, the main equipment parameters of the five-stand cold tandem rolling mill are collected, mainly including: 1-5# stand work roll diameter D wi ={538.1,474.8,495.1,527.2,528.5}mm, 1-5# rack support roller diameter D bi ={1218, 1228.2, 1325.4, 1235, 1304.9} mm, 1-5# frame work roll roll distribution ΔD wij =0 (j is the number of strip elements), 1-5# frame support roller roll profile distribution ΔD bij =0, 1-5# frame work roll body length L wi =1220mm, 1-5# frame support roller body length L bi =1092mm, 1-5# frame work roll bending cylinder center distance l wi =2100mm, 1-5# frame support roller press down screw center distance l bi =2100mm;
[0050] Subsequently, in step 2, the process characteristic parameters of the five-stand cold tandem rolling unit...
Embodiment 2
[0068] First, in step 1, the main equipment parameters of the five-stand cold tandem rolling mill are collected, mainly including: 1-5# stand work roll diameter D wi ={525.7,482.3,493.4,526.1,522.3}mm, 1-5# rack support roller diameter D bi ={1275.4, 1229.9, 1226.9, 1297, 1214} mm, 1-5# frame work roll distribution ΔD wij =0 (j is the number of strip elements), 1-5# frame support roller roll profile distribution ΔD bij =0, 1-5# frame work roll body length L wi =1220mm, 1-5# frame support roller body length L bi =1092mm, 1-5# frame work roll bending cylinder center distance l wi =2100mm, 1-5# frame support roller press down screw center distance l bi =2100mm;
[0069] Subsequently, in step 2, the process characteristic parameters of the five-stand cold tandem rolling unit are collected, mainly including: the allowable maximum rolling pressure P of 1-5# stands maxi =2000t, 1-5# stand allowable maximum rolling power F maxi =5000kw, 1-5# frame work roll maximum positive ben...
PUM
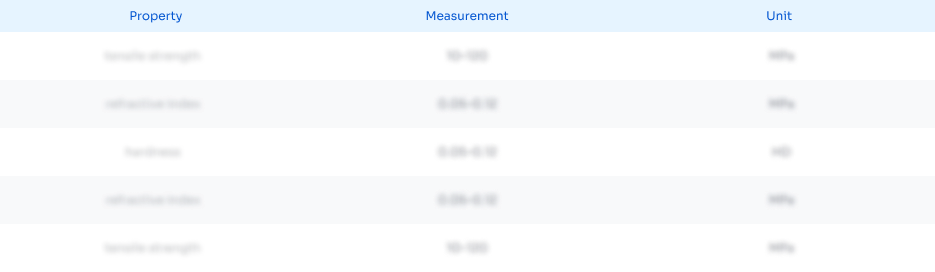
Abstract
Description
Claims
Application Information

- Generate Ideas
- Intellectual Property
- Life Sciences
- Materials
- Tech Scout
- Unparalleled Data Quality
- Higher Quality Content
- 60% Fewer Hallucinations
Browse by: Latest US Patents, China's latest patents, Technical Efficacy Thesaurus, Application Domain, Technology Topic, Popular Technical Reports.
© 2025 PatSnap. All rights reserved.Legal|Privacy policy|Modern Slavery Act Transparency Statement|Sitemap|About US| Contact US: help@patsnap.com