Melt differential electrostatic spinning device and process
A technology of melt differentiation and electrospinning, which is applied in textiles and papermaking, filament/thread forming, fiber processing, etc. It can solve the problems that are difficult to be suitable for industrial application, complex structure, high energy consumption, etc., and achieve simple device and process Ease of operation, simple structure and high output
- Summary
- Abstract
- Description
- Claims
- Application Information
AI Technical Summary
Problems solved by technology
Method used
Image
Examples
Embodiment 1
[0030] Such as figure 1As shown, the melt differential electrospinning device of the present invention mainly includes a melt differential electrospinning nozzle and a multi-electric field coupling strong drafting device.
[0031] The melt differential electrospinning nozzle is mainly composed of a splitter plate 1, a nut 2, a spring washer 3, an air duct positioning pin 4, a screw 5, a nozzle body positioning pin 6, a nozzle body 7, an air duct 8, a heating device 9, and a temperature sensor 10. Cone nozzle 11 and ground electrode 17. The nozzle body 7 and the distribution plate 1 are positioned by the nozzle body positioning pin 6 and connected with the screw 5. The inlet of the inclined flow channel on the nozzle body 7 communicates with the outlet of the distribution channel on the distribution plate 1; the air duct 8 is installed on the nozzle body 7 and the distribution channel In the inner hole of the plate 1, there is an annular gap between the outer surface of the ai...
Embodiment 2
[0036] Such as figure 2 As shown, the structure, working principle and effect of this embodiment are basically the same as those of Embodiment 1, the difference is that in the melt differential electrospinning nozzle, the inner cone nozzle 11 can also be replaced with the outer cone nozzle 24, and the outer cone nozzle The surface nozzle 24 is connected to the bottom end of the air duct 8 through threads, the nozzle body 7 is connected to the ground electrode 17, and the rest of the structure is the same as that of the aforementioned melt differential electrospinning nozzle.
[0037] The multi-electric field coupling strong drafting device is composed of three layers of electrode plates. The outer cone nozzle 24 is equipped with electrode plate 1 12, electrode plate 3 19, and electrode plate 4 20 in turn. The three electrode plates are electrode plates with holes in the middle. , the electrode plate one 12 is connected with the high-voltage positive terminal of the high-volta...
PUM
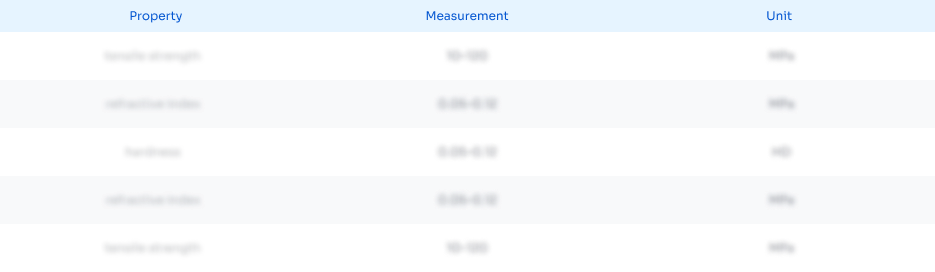
Abstract
Description
Claims
Application Information

- R&D
- Intellectual Property
- Life Sciences
- Materials
- Tech Scout
- Unparalleled Data Quality
- Higher Quality Content
- 60% Fewer Hallucinations
Browse by: Latest US Patents, China's latest patents, Technical Efficacy Thesaurus, Application Domain, Technology Topic, Popular Technical Reports.
© 2025 PatSnap. All rights reserved.Legal|Privacy policy|Modern Slavery Act Transparency Statement|Sitemap|About US| Contact US: help@patsnap.com