Melting film equipment suitable for flexible polyurethane foam coils and method for realizing melting film based on the melting film equipment
A technology of soft foam and foam coil, which is applied in the field of high-efficiency and safe melting film equipment and its processing, can solve the problems of coil deformation, uneven distribution of blasting force, damage, etc., and achieve the effect of eliminating material waste and good overall quality
- Summary
- Abstract
- Description
- Claims
- Application Information
AI Technical Summary
Problems solved by technology
Method used
Image
Examples
Embodiment 1
[0030] A high-efficiency and safe melting film equipment for flexible polyurethane foam coils, which consists of: a circular pressure-resistant container 1, the circular pressure-resistant container is connected to a circular quick-opening upper door 3 through a circular chuck 2, and the The circular quick-opening upper door is connected to the lifting and translation device 4; wherein, the bottom of the circular pressure-resistant container is connected to a group of gas injection ports 5, and the circular quick-opening upper door is connected to the air suction port 6.
[0031] The circular pressure-resistant container is used to hold the foam roll 7, and is used as a place for pumping, injecting, and igniting and blasting.
Embodiment 2
[0033] According to the high-efficiency and safe melting film equipment for flexible polyurethane foam coils described in Example 1, the circular pressure-resistant container also has an isolation device 8, and the cylinder wall of the circular pressure-resistant container also has a Group monitoring device9.
[0034] The monitoring device also has a pressure sensor and a data processing system.
Embodiment 3
[0036] A processing method of high-efficiency and safe melting film equipment for flexible polyurethane foam coils. The first step is to start the lifting and translation device to open the circular quick-opening door, and install the foam coil with the movable igniter 10 in the center together with the isolation device. into a circular pressure vessel;
[0037] In the second step, after closing the circular quick-opening door, lock it with the circular pressure-resistant container with a circular chuck, and at this time, use the pumping system to vacuumize the container through the pumping port;
[0038] In the third step, after vacuuming, use the gas injection system to inject hydrogen and oxygen through the gas injection port;
[0039] The fourth step, after the gas injection is completed, inject inert gas between the foam coil and the circular pressure-resistant container through the gas injection port, then ignite and explode, and open the circular quick-opening valve aft...
PUM
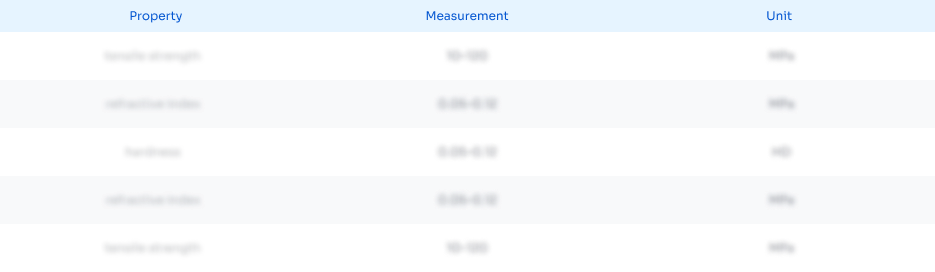
Abstract
Description
Claims
Application Information

- R&D
- Intellectual Property
- Life Sciences
- Materials
- Tech Scout
- Unparalleled Data Quality
- Higher Quality Content
- 60% Fewer Hallucinations
Browse by: Latest US Patents, China's latest patents, Technical Efficacy Thesaurus, Application Domain, Technology Topic, Popular Technical Reports.
© 2025 PatSnap. All rights reserved.Legal|Privacy policy|Modern Slavery Act Transparency Statement|Sitemap|About US| Contact US: help@patsnap.com