A Prediction Method of Tensile Strength of Composite π-shaped Bonded Connection Structure Based on Average Failure Index
A composite material and connection structure technology, applied in the direction of electrical digital data processing, special data processing applications, instruments, etc., can solve the problems of large calculation scale and long calculation cycle, so as to reduce test cost, save calculation cost and time, shorten The effect of development cycle
- Summary
- Abstract
- Description
- Claims
- Application Information
AI Technical Summary
Problems solved by technology
Method used
Image
Examples
Embodiment Construction
[0035] Such as figure 2 Shown, the concrete realization of the inventive method is:
[0036] 1. Based on the finite element analysis software ABAQUS, the geometric model of the π joint is established according to the geometric parameters of the composite material π-shaped adhesive joint structure.
[0037] According to the structural geometric parameters of composite material π joints, use the finite element analysis software ABAQUS to establish a 3D geometric model of π joints; define material properties and local material directions, and divide the geometric model according to the thickness of each layer, create composite material layers and define When defining the ply angle, it is necessary to establish the corresponding local coordinate system according to the specific situation.
[0038] 2. Determine the tensile load and boundary conditions of the geometric model of the composite π-joint according to the stress of the integrated composite structure.
[0039] Carry out...
PUM
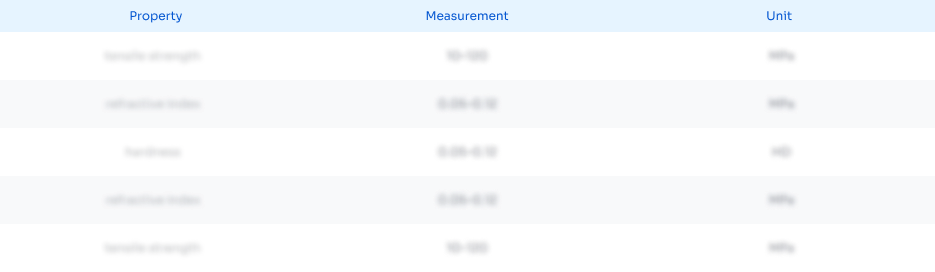
Abstract
Description
Claims
Application Information

- R&D Engineer
- R&D Manager
- IP Professional
- Industry Leading Data Capabilities
- Powerful AI technology
- Patent DNA Extraction
Browse by: Latest US Patents, China's latest patents, Technical Efficacy Thesaurus, Application Domain, Technology Topic, Popular Technical Reports.
© 2024 PatSnap. All rights reserved.Legal|Privacy policy|Modern Slavery Act Transparency Statement|Sitemap|About US| Contact US: help@patsnap.com