High-hardness and extremely-cold-resistant sole material and preparation method thereof
A shoe sole material and high hardness technology, applied in the field of rubber processing, can solve the problems of high material price and complicated manufacturing process, and achieve the effect of low cost, simple method and good use effect
- Summary
- Abstract
- Description
- Claims
- Application Information
AI Technical Summary
Problems solved by technology
Method used
Image
Examples
Embodiment 1
[0031] Embodiment 1 of the present invention: high hardness, extremely cold-resistant shoe sole material, calculate by weight, comprise 60 parts of natural rubber, 40 parts of butadiene rubber, 2 parts of sulfur, 30 parts of high styrene, 4.1 parts of vulcanization accelerator, vulcanization 5 parts of active agent, 1.8 parts of anti-aging agent, 11 parts of softener and 58 parts of filling and strengthening agent.
[0032] The preparation method of high hardness, extremely cold-resistant shoe sole material, each component is taken according to the above-mentioned parts by weight, and the operation steps are as follows:
[0033] (1) Mastication: Masticate natural rubber and high styrene together to make its Vickers plasticity reach 0.53-0.58 to obtain plastication rubber;
[0034] (2) Master batch: Mix half of the plasticized rubber with 50 parts of filler and reinforcing agent and butadiene rubber to prepare the master batch;
[0035] (3) Mixing: put the remaining plasticize...
Embodiment 2
[0038]Embodiment 2 of the present invention: high hardness, extremely cold-resistant shoe sole material, calculate by weight, comprise 30 parts of natural rubber, 70 parts of butadiene rubber, 1 part of vulcanizing agent, 20 parts of high styrene, 1 part of vulcanization accelerator, 3 parts of vulcanization active agent, 1 part of anti-aging agent, 5 parts of softener and 70 parts of filling and reinforcing agent.
[0039] The preparation method is the same as in Example 1.
Embodiment 3
[0040] Embodiment 3 of the present invention: high hardness, extremely cold-resistant shoe sole material, calculate by weight, comprise 90 parts of natural rubbers, 10 parts of butadiene rubbers, 3 parts of vulcanizing agents, 40 parts of high styrene, 5 parts of vulcanization accelerators, 5 parts of vulcanization active agent, 2 parts of anti-aging agent, 15 parts of softener and 70 parts of filling and reinforcing agent.
[0041] The preparation method is the same as in Example 1.
PUM
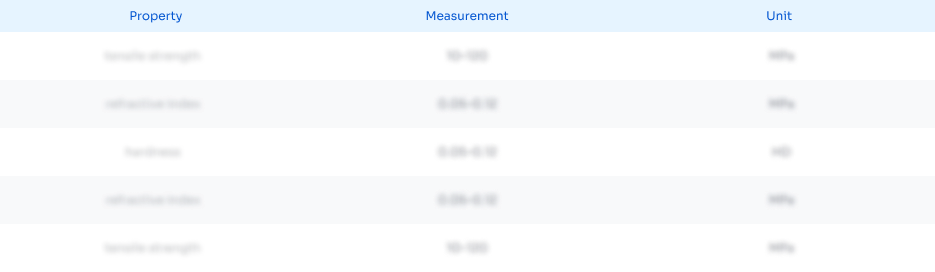
Abstract
Description
Claims
Application Information

- R&D Engineer
- R&D Manager
- IP Professional
- Industry Leading Data Capabilities
- Powerful AI technology
- Patent DNA Extraction
Browse by: Latest US Patents, China's latest patents, Technical Efficacy Thesaurus, Application Domain, Technology Topic, Popular Technical Reports.
© 2024 PatSnap. All rights reserved.Legal|Privacy policy|Modern Slavery Act Transparency Statement|Sitemap|About US| Contact US: help@patsnap.com