Method for preparing butadiene by multistage oxidative dehydrogenation of butene
An oxidative dehydrogenation, butadiene technology, applied in chemical instruments and methods, organic chemistry, hydrocarbons, etc., can solve the problems of uneven catalyst temperature, poor butadiene selectivity, short regeneration cycle, etc., to improve the conversion efficiency and selectivity, increased reaction stages, and savings in product yields
- Summary
- Abstract
- Description
- Claims
- Application Information
AI Technical Summary
Problems solved by technology
Method used
Image
Examples
Embodiment 1
[0036] A 200,000 tons / year butene oxidative dehydrogenation to butadiene plant adopts figure 1 The process technology, the reactor is two-stage, and the two-stage reactors are isothermal tubular fixed-bed reactors. The iron-based oxide catalysts are filled in the tubes of the two-stage reactors. The main components include iron, zinc, magnesium, molar The ratio is: Fe:Zn:Mg=10:3:5, prepared by co-precipitation method, the main crystal phase is ZnFe 2 o 4 Spinel, the primary reactor and the secondary reactor have the same structure, the size is Φ4500×6000mm, the tubes are Φ50×6000mm, the number of tubes is 4000, and the heat exchange area is 3900m 2 , the shell side of the primary reactor and the secondary reactor are divided into two upper and lower heat removal chambers by a partition perpendicular to the tubes. The heat removal medium is heat transfer oil. The total amount of butene is 40000kg / h, the total amount of air is 72000kg / h, the butene raw material is divided into...
Embodiment 2
[0041] A 200,000 tons / year butene oxidative dehydrogenation to butadiene plant adopts figure 1 The process technology, the reactor is two-stage, and the two-stage reactors are isothermal tubular fixed-bed reactors. The iron-based oxide catalysts are filled in the tubes of the two-stage reactors. The main components include iron, zinc, magnesium, molar The ratio is: Fe:Zn:Mg=10:3:5, prepared by co-precipitation method, the main crystal phase is ZnFe 2 o 4 Spinel, the primary reactor and the secondary reactor have the same structure, the size is Φ4500×6000mm, the tubes are Φ50×6000mm, the number of tubes is 4000, and the heat exchange area is 3900m 2 , the primary reactor and the secondary reactor shell side are divided into 4 heat removal chambers by the partitions perpendicular to the tubes. The flow rate of butene is 40000kg / h, the total amount of air is 72000kg / h, the butene raw material is divided into two parts, the flow rate of butene in the first stage is 26000kg / h, th...
Embodiment 3
[0046] A 200,000 tons / year butene oxidative dehydrogenation to butadiene plant adopts figure 1 The process technology, the reactor is two-stage, and the two-stage reactors are isothermal tubular fixed-bed reactors. The iron-based oxide catalysts are filled in the tubes of the two-stage reactors. The main components include iron, zinc, magnesium, molar The ratio is: Fe: Zn: Mg=10:4:6, prepared by co-precipitation method, the main crystal phase is ZnFe 2 o 4 Spinel, the primary reactor and the secondary reactor have the same structure, the size is Φ4500×6000mm, the tubes are Φ50×6000mm, the number of tubes is 4000, and the heat exchange area is 3900m 2 , the first-stage reactor and the second-stage reactor shell side are divided into two heat removal chambers by the partitions perpendicular to the tubes. The heat removal medium is molten salt. The temperature of the molten salt inlet is 350 ° C. 40000kg / h, the total air volume is 72000kg / h, the butene raw material is divided i...
PUM
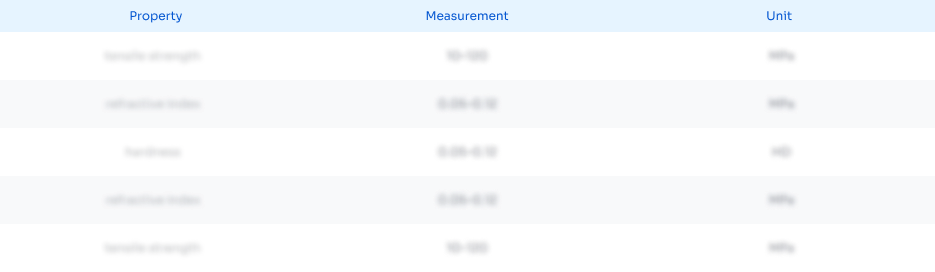
Abstract
Description
Claims
Application Information

- R&D
- Intellectual Property
- Life Sciences
- Materials
- Tech Scout
- Unparalleled Data Quality
- Higher Quality Content
- 60% Fewer Hallucinations
Browse by: Latest US Patents, China's latest patents, Technical Efficacy Thesaurus, Application Domain, Technology Topic, Popular Technical Reports.
© 2025 PatSnap. All rights reserved.Legal|Privacy policy|Modern Slavery Act Transparency Statement|Sitemap|About US| Contact US: help@patsnap.com