Flow line production system of hot melt adhesive particles
A production system and hot melt adhesive technology, which are applied in solid separation, sieves, grids, etc., can solve the problems of increasing the complexity of production equipment and manufacturing costs, occupying a large production workshop area, and low granulation efficiency. , to achieve the effect of reducing daily production and operation costs, high production efficiency, and saving environmental protection effects
- Summary
- Abstract
- Description
- Claims
- Application Information
AI Technical Summary
Problems solved by technology
Method used
Image
Examples
Embodiment Construction
[0028] Such as figure 1 As shown, the assembly line production system of a kind of hot-melt colloidal granule of the present invention comprises hot-melt stirring reaction device 1, constant temperature filter screen device 2, extruding pelletizing device 3, cooling pipeline device 4, colloidal granule and water separation Drying device 5, rubber particle air-drying packaging device 6, cooling water treatment device 7, wherein
[0029] Such as figure 2 , image 3 As shown, the constant temperature filter device 2 includes a rubber input end 21, a rubber output end 22, a left mounting block 23, a right mounting block 24, a filter mechanism 25 and a cylinder 26, wherein one end of the rubber input end 21 is connected to the The left mounting block 23 is connected, and the other end of the rubber input end 21 is connected with the molten rubber output port provided on the hot-melt stirring reaction device 1 through a metal pipe; the rubber output end 22 is connected with the r...
PUM
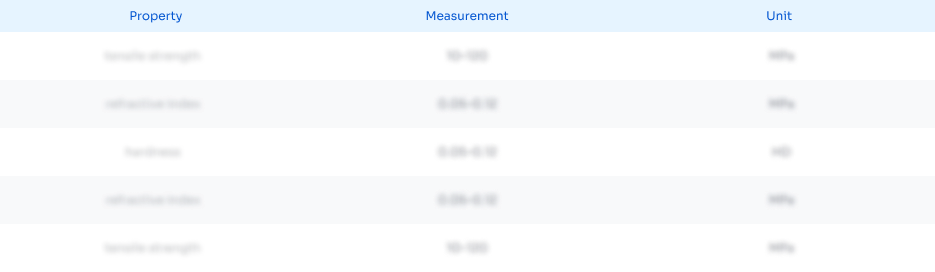
Abstract
Description
Claims
Application Information

- Generate Ideas
- Intellectual Property
- Life Sciences
- Materials
- Tech Scout
- Unparalleled Data Quality
- Higher Quality Content
- 60% Fewer Hallucinations
Browse by: Latest US Patents, China's latest patents, Technical Efficacy Thesaurus, Application Domain, Technology Topic, Popular Technical Reports.
© 2025 PatSnap. All rights reserved.Legal|Privacy policy|Modern Slavery Act Transparency Statement|Sitemap|About US| Contact US: help@patsnap.com