Plate material processing system
A sheet metal processing and sheet metal technology, applied in metal processing, metal processing equipment, manufacturing tools, etc., can solve problems such as increasing production costs and operating costs, limiting the configuration and difficulty of the location where product sheets are transported out
- Summary
- Abstract
- Description
- Claims
- Application Information
AI Technical Summary
Problems solved by technology
Method used
Image
Examples
Embodiment Construction
[0028] One embodiment of the present invention will be described with reference to the drawings. like figure 1As shown, the board processing system includes: a board processing machine 1 , a loader 2 , and a system control device 3 . The sheet material processing machine 1 is a member for processing the raw material sheet W1, and is a punch press in the present embodiment. The loader 2 loads the raw material sheet W1 into the sheet processing machine 1 and unloads the product sheet W2 processed by the sheet processing machine 1 . The system control device 3 controls the panel processing machine 1 and the loader 2 which are machine parts of the panel processing system.
[0029] A plate processing machine 1 consisting of a punch press includes a table 5 on which a plate is placed, a processing head 6 for punching a plate on the table 5, and a plate that is placed on the table 5 in the front-back direction (Y axis) and the left-right direction. (X-axis) moving plate feeding me...
PUM
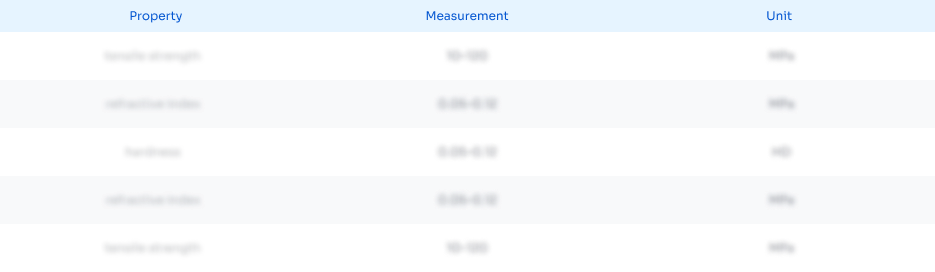
Abstract
Description
Claims
Application Information

- R&D Engineer
- R&D Manager
- IP Professional
- Industry Leading Data Capabilities
- Powerful AI technology
- Patent DNA Extraction
Browse by: Latest US Patents, China's latest patents, Technical Efficacy Thesaurus, Application Domain, Technology Topic, Popular Technical Reports.
© 2024 PatSnap. All rights reserved.Legal|Privacy policy|Modern Slavery Act Transparency Statement|Sitemap|About US| Contact US: help@patsnap.com