Method for preparing ultralow-metallic-element ultrahigh-purity quartz through mixed acid hot-pressing leaching reaction
A hot-pressing leaching, metal element technology, applied in the direction of silicon dioxide, silicon oxide, etc., can solve the problems of limited reserves and uneven distribution of high-quality quartz resources, and achieve the effect of increasing the contact surface area
- Summary
- Abstract
- Description
- Claims
- Application Information
AI Technical Summary
Problems solved by technology
Method used
Image
Examples
Embodiment 1
[0058] (1) Crushing and grading
[0059] The vein quartz raw ore is crushed and graded to prepare vein quartz sand with a particle size of 96-212 μm, and the vein quartz sand SiO 2 The purity is 99.8-99.9%, and the content of impurity metal elements: Al20-160μg·g -1 , Fe10~210μg·g -1 , Ti6~35μg·g -1 , Ca5~70μg·g -1 , Mg0.5~20μg·g -1 , Li2~15μg·g -1 , Na15~75μg·g -1 , K15~75μg·g -1 ;
[0060] (2) Magnetic separation
[0061] The sample obtained in step (1) is subjected to high-gradient pulsating strong magnetic separation under the conditions of pulp concentration of 35wt%, magnetic field strength of 0.8T, and pulsation intensity of 200r / min, and non-magnetic products are dried for use;
[0062] (3) Three-stage priority reverse flotation
[0063] Reverse flotation of the non-magnetic product obtained in step (2), the three-stage preferential reverse flotation refers to: one-stage reverse flotation to separate iron minerals, after drug removal, second-stage reverse flo...
Embodiment 2
[0073] (1) Crushing and grading
[0074] The vein quartz raw ore is crushed and graded to prepare vein quartz sand with a particle size of 96-212 μm, and the vein quartz sand SiO 2 The purity is 99.8-99.9%, and the content of impurity metal elements: Al20-160μg·g -1 , Fe10~210μg·g -1 , Ti6~35μg·g -1 , Ca5~70μg·g -1 , Mg0.5~20μg·g -1 , Li2~15μg·g -1 , Na15~75μg·g -1 , K15~75μg·g -1 ;
[0075] (2) Magnetic separation
[0076] The sample obtained in step (1) is subjected to high-gradient pulsating strong magnetic separation under the conditions of pulp concentration of 35wt%, magnetic field strength of 1.2T, and pulsation intensity of 300r / min, and non-magnetic products are dried for use;
[0077] (3) Three-stage priority reverse flotation
[0078] Reverse flotation of the non-magnetic product obtained in step (2), the three-stage preferential reverse flotation process is: one stage of reverse flotation to separate iron minerals, after drug removal, the second stage of re...
Embodiment 3
[0088] (1) Crushing and grading
[0089] The vein quartz raw ore is crushed and graded to prepare vein quartz sand with a particle size of 96-212 μm, and the vein quartz sand SiO 2 The purity is 99.8-99.9%, and the content of impurity metal elements: Al20-160μg·g -1 , Fe10~210μg·g -1 , Ti6~35μg·g -1 , Ca5~70μg·g -1 , Mg0.5~20μg·g -1 , Li2~15μg·g -1 , Na15~75μg·g -1 , K15~75μg·g -1 ;
[0090] (2) Magnetic separation
[0091] The sample obtained in step (1) is subjected to high-gradient pulsating strong magnetic separation under the conditions of pulp concentration of 35wt%, magnetic field strength of 1.2T, and pulsation intensity of 300r / min, and non-magnetic products are dried for use;
[0092] (3) Three-stage priority reverse flotation
[0093] Reverse flotation of the non-magnetic product obtained in step (2), the three-stage preferential reverse flotation process is: one stage of reverse flotation to separate iron minerals, after drug removal, the second stage of ...
PUM
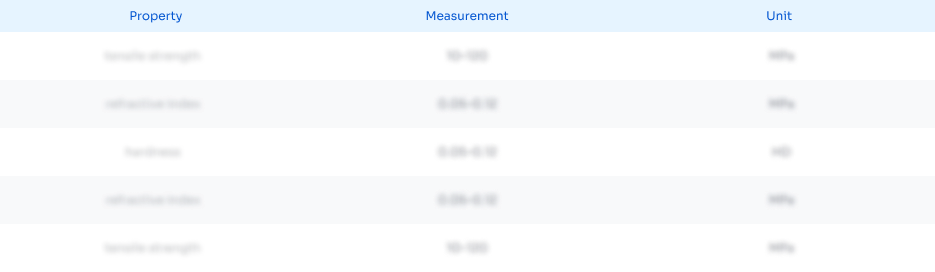
Abstract
Description
Claims
Application Information

- Generate Ideas
- Intellectual Property
- Life Sciences
- Materials
- Tech Scout
- Unparalleled Data Quality
- Higher Quality Content
- 60% Fewer Hallucinations
Browse by: Latest US Patents, China's latest patents, Technical Efficacy Thesaurus, Application Domain, Technology Topic, Popular Technical Reports.
© 2025 PatSnap. All rights reserved.Legal|Privacy policy|Modern Slavery Act Transparency Statement|Sitemap|About US| Contact US: help@patsnap.com