High-voltage winding middle inlet wire structure K wire lead cold pressing technology
A high-voltage winding and K-line technology, applied in coil manufacturing, cable joints, connections where permanent deformation works, etc., can solve problems such as many shortcomings and difficulties, and achieve the goal of reducing labor intensity, improving product quality, and eliminating potential safety hazards. Effect
- Summary
- Abstract
- Description
- Claims
- Application Information
AI Technical Summary
Problems solved by technology
Method used
Examples
Embodiment Construction
[0007] 1. The process of K-line connection: selection of connecting pipe→transformation of connecting pipe→cable pretreatment→cold crimping.
[0008] 2. The method of connecting the K line: (1) Select the type of connecting pipe according to the cross section of the K line. The sum of the cross sections of the two cables is equal to the sum of the internal cross sections of the connecting pipe to ensure matching.
[0009] (2) Ensure that the upper and lower K wires that need to be crimped can pass through the connecting pipe at the same time, and the crimped joints should be treated before insulation wrapping. First wrap the joints into an olive shape with aluminum foil, and then wrap them with metal wrinkles , to ensure that the shape of the electrode at the crimp is uniform and the contact resistivity is minimal.
[0010] (3) Process the connecting pipe: turn the two ends of the connecting pipe into bullnose so that the two ends are hemispherical after crimping to avoid sha...
PUM
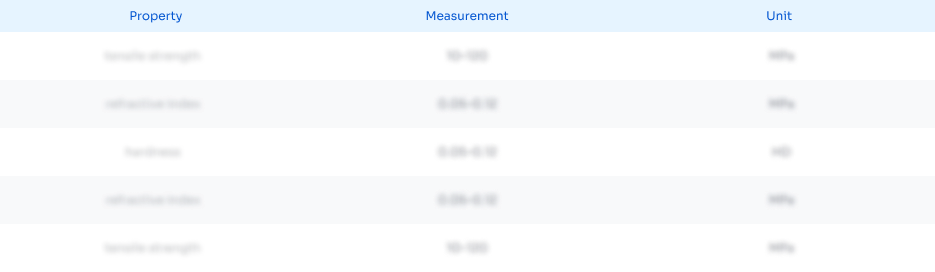
Abstract
Description
Claims
Application Information

- R&D
- Intellectual Property
- Life Sciences
- Materials
- Tech Scout
- Unparalleled Data Quality
- Higher Quality Content
- 60% Fewer Hallucinations
Browse by: Latest US Patents, China's latest patents, Technical Efficacy Thesaurus, Application Domain, Technology Topic, Popular Technical Reports.
© 2025 PatSnap. All rights reserved.Legal|Privacy policy|Modern Slavery Act Transparency Statement|Sitemap|About US| Contact US: help@patsnap.com