A Method for Rapid Transition of Finite Element 3D Model Mesh
A three-dimensional model and finite element technology, applied in special data processing applications, instruments, electrical digital data processing, etc., can solve problems such as complex operation, small transition ratio, and difficulty in realizing finite element simulation of large components, achieving remarkable efficiency, The effect of saving the total number of grids, division efficiency and transition ratio improvement
- Summary
- Abstract
- Description
- Claims
- Application Information
AI Technical Summary
Problems solved by technology
Method used
Image
Examples
specific Embodiment approach 1
[0031] Specific implementation mode one: combine Figure 1 to Figure 5 Describe this implementation mode, this implementation mode is realized through the following steps:
[0032] Step 1. First, divide the three-dimensional model of large and complex components into different regions:
[0033] According to the size of the calculated data change gradient of different parts of the component, it is divided into key area A, transition area B and non-key area C;
[0034] Step 2: Carry out grid division for key area A:
[0035] Divide several cubic or cuboid grids in the key area A, and the grids in the key area A should be dense; the key area A is the calculation data change gradient or key areas (such as stress concentration parts), in order to better reflect the data Change law, the finite element calculation has higher requirements on the grid quality of this area, and a relatively dense grid is used, so it is necessary to focus on dividing the key area A separately;
[0036...
specific Embodiment approach 2
[0044] Specific implementation mode two: combination image 3 Describe this embodiment. In this embodiment, in step 3, the acute angle between the left bisecting slope O-M and the concave lower end surface is 45°, and the acute angle between the right bisecting slope O-N and the concave lower end surface is 45°. Other steps are the same as in the first embodiment.
specific Embodiment approach 3
[0045] Specific implementation mode three: combination Figure 4 Describe this embodiment. In this embodiment, in step 3, the grid size inside the transition area B matches the square grid size of the key area A. Other steps are the same as those in Embodiment 1 or 2.
PUM
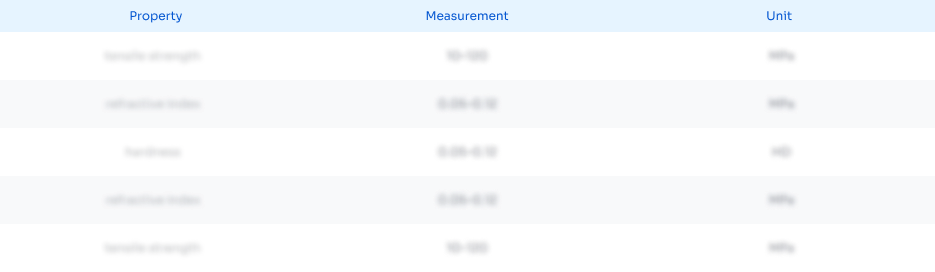
Abstract
Description
Claims
Application Information

- Generate Ideas
- Intellectual Property
- Life Sciences
- Materials
- Tech Scout
- Unparalleled Data Quality
- Higher Quality Content
- 60% Fewer Hallucinations
Browse by: Latest US Patents, China's latest patents, Technical Efficacy Thesaurus, Application Domain, Technology Topic, Popular Technical Reports.
© 2025 PatSnap. All rights reserved.Legal|Privacy policy|Modern Slavery Act Transparency Statement|Sitemap|About US| Contact US: help@patsnap.com