Injection molding method of plastic worm wheel and injection mold assembly
A technology of injection molds and worm gears, which is applied to gears, household appliances, and other household appliances. It can solve problems such as high cost, long ring gear cycle, and poor product accuracy, and achieve low cost, short processing cycle, and stable dimensions.
- Summary
- Abstract
- Description
- Claims
- Application Information
AI Technical Summary
Problems solved by technology
Method used
Image
Examples
Embodiment 1
[0041] like Figures 3 to 7 As shown, the lateral sliding mechanism is an inclined top 501, the head of the inclined top is in the shape of fan-shaped teeth, and the two sides of the inclined top head 502 are slopes 503 that cooperate with the adjacent inclined tops, which are arranged in a circle. The slanted top head 502 of the fan-shaped tooth shape of several slanted tops 501, the front mold core 301 of the fixed mold part 401 and the rear mold core 302 of the movable mold part 402 are combined into the mold cavity 303 of the plastic worm wheel mold; The back 504 of 501 is provided with a T-shaped protrusion, and the guide angle of the inclined top 501 is 5°-10° (preferably 8°) away from the center of the cavity 303 relative to the ejection direction of the ejection mechanism; The inclined top 501 is placed in the inclined top guide groove 304, and the inclined top guide groove 304 is provided with a T-shaped groove which is combined with the T-shaped protrusion of the inc...
Embodiment 2
[0048] like Figures 8 to 14 As shown, the lateral sliding mechanism is a slider 106, the head of the slider 106 is in the shape of a fan-shaped tooth, and the two sides of the slider head 107 are slopes matching with adjacent sliders, and several sliders arranged in a circle The slider head 107 of the fan-shaped tooth shape of the block, the front mold core 301 of the fixed mold part 401 and the rear mold core 302 of the movable mold part 402 are combined to form the cavity 303 of the plastic worm gear mold; the slide block 106 is placed In the slider guide groove 801, the slider guide groove 801 leaves a space for the slider 106 to slide; the middle part of the slider is provided with an oblique groove 110, and the oblique groove 110 extends away from the top of the slider. The center of the cavity 303 extends to the inside of the slider 106 ; the lower end of the front mold core 301 of the fixed mold part 401 is fixed with a locking block 802 that fits with the oblique groo...
PUM
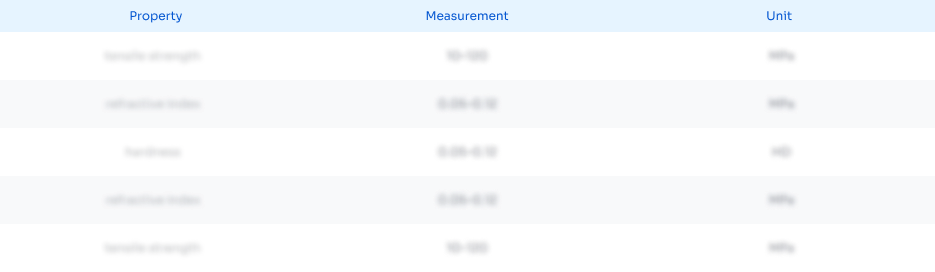
Abstract
Description
Claims
Application Information

- R&D
- Intellectual Property
- Life Sciences
- Materials
- Tech Scout
- Unparalleled Data Quality
- Higher Quality Content
- 60% Fewer Hallucinations
Browse by: Latest US Patents, China's latest patents, Technical Efficacy Thesaurus, Application Domain, Technology Topic, Popular Technical Reports.
© 2025 PatSnap. All rights reserved.Legal|Privacy policy|Modern Slavery Act Transparency Statement|Sitemap|About US| Contact US: help@patsnap.com