Deviation value control method of cold-rolled hot-dip galvanized coating uniformity
A control method and technology of deviation value, applied in hot dip plating process, coating, metal material coating process, etc., can solve the problems of insignificant effect, inability to dynamically change, and restricting the ability to adjust the uniformity of the coating layer.
- Summary
- Abstract
- Description
- Claims
- Application Information
AI Technical Summary
Problems solved by technology
Method used
Image
Examples
Embodiment Construction
[0052] Below by embodiment the present invention will be further described.
[0053] The embodiment of the present invention takes the cold continuous hot-dip galvanizing production unit as an example, as figure 1 As shown, the annual production capacity is 450,000 tons, and its products are aimed at the middle and high-end automobile and home appliance board markets. The limit value of the movement of the lip motor is defined in practical applications: when the lip gap reference value is less than 0.4mm, the lip motor is prohibited from moving downward, and only upward movement is allowed; when the lip gap reference value is greater than 2.5mm, the lip motor is prohibited from moving upward , only downward movement is allowed. For the control process of galvanized layer thickness deviation value, see figure 2 . Such as image 3 As shown, the actual application of m=12 lip motors on the upper and lower surfaces of the air knife controls the lip seam value along the width ...
PUM
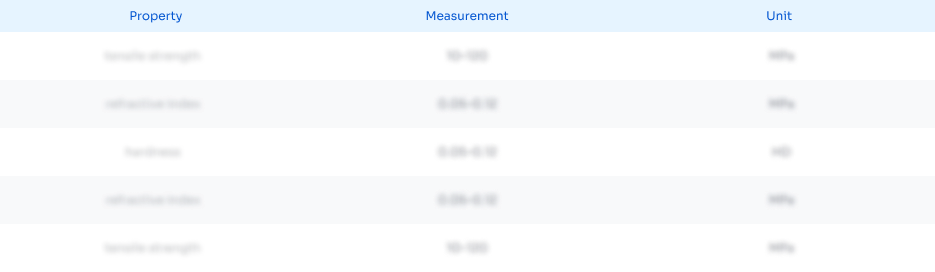
Abstract
Description
Claims
Application Information

- R&D
- Intellectual Property
- Life Sciences
- Materials
- Tech Scout
- Unparalleled Data Quality
- Higher Quality Content
- 60% Fewer Hallucinations
Browse by: Latest US Patents, China's latest patents, Technical Efficacy Thesaurus, Application Domain, Technology Topic, Popular Technical Reports.
© 2025 PatSnap. All rights reserved.Legal|Privacy policy|Modern Slavery Act Transparency Statement|Sitemap|About US| Contact US: help@patsnap.com