Method for reducing emission of flue gas pollutants generated by sintering high sulfur containing pyrites
A high-pyrite ore and pollutant technology, applied in the field of flue gas pollutant emission reduction of high-pyrite ore sintering, can solve the problems of blast furnace ironmaking adverse effects, high concentration, sulfur enrichment, etc., to prolong the high temperature time, Effects of reducing free CaO content and increasing sintering temperature
- Summary
- Abstract
- Description
- Claims
- Application Information
AI Technical Summary
Problems solved by technology
Method used
Image
Examples
Embodiment 1
[0027] For the mixed iron ore with a sulfur content of 0.1%, quicklime accounting for 4% of the total mass of the sintering mixture is mixed in the batching process. The CaO content of the quicklime is 82% and the activity is 400ml; the nine-roller cloth is used to make the sintering machine The mass percentage of fuel in the surface material is 0.4% higher than that of the bottom material; the ignition intensity is 20% higher than that of conventional sintering during ignition, and the ignition temperature is 1200°C; the flue gas part of the tail wind box of the sintering machine will account for 1 / 3 of the length of the sintering machine Circulate to the surface of the sintered material, that is, SO at the tail of the sintering machine 2 The flue gas from the two wind boxes with the highest concentration is sent to the desulfurization system for desulfurization, and the flue gas from the remaining wind boxes at the tail is circulated to the fume hood on the sintering material...
Embodiment 2
[0029] For the mixed iron ore with a sulfur content of 0.3%, quicklime accounting for 6% of the total mass of the sintering mixture is mixed in the batching. The CaO content of the quicklime is 88% and the activity is 550ml; the air flow distribution is used to make the surface of the sintering machine The mass percentage of fuel in the material is 0.8% higher than that of the bottom material; the ignition intensity during ignition is 30% higher than that of conventional sintering, and the ignition temperature is 1250°C; the flue gas of the tail bellows of the sintering machine, which accounts for 1 / 2 of the length of the sintering machine, is partially circulated To the surface of the sintered material, that is, the SO at the tail of the sintering machine 2 The flue gas from the three bellows with the highest concentration is sent to the desulfurization system for desulfurization, and the flue gas from the remaining bellows at the tail is circulated to the fume hood on the sin...
PUM
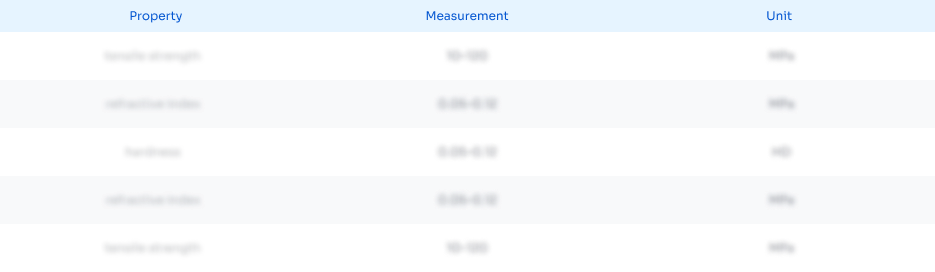
Abstract
Description
Claims
Application Information

- R&D
- Intellectual Property
- Life Sciences
- Materials
- Tech Scout
- Unparalleled Data Quality
- Higher Quality Content
- 60% Fewer Hallucinations
Browse by: Latest US Patents, China's latest patents, Technical Efficacy Thesaurus, Application Domain, Technology Topic, Popular Technical Reports.
© 2025 PatSnap. All rights reserved.Legal|Privacy policy|Modern Slavery Act Transparency Statement|Sitemap|About US| Contact US: help@patsnap.com