Dielectric film preparation method for improving capacity extraction rate of solid electrolyte tantalum capacitor
A technology of solid electrolyte and tantalum capacitors, which is applied in the direction of solid electrolytic capacitors, capacitor dielectric layers, capacitor parts, etc., can solve the problems of poor fluidity of tantalum powder, uneven pressing density, narrow pores of anode tantalum block, etc. efficiency, improve the effect of impregnation process
- Summary
- Abstract
- Description
- Claims
- Application Information
AI Technical Summary
Problems solved by technology
Method used
Image
Examples
Embodiment 1
[0015] 1) Press the tantalum powder with a specific volume of 70,000 V·μF / g into a 10V470μF anode tantalum block according to the conventional method;
[0016] 2) Sintering the anode tantalum block at high temperature according to the conventional method;
[0017] 3) Immerse the high-temperature sintered anode tantalum block in the manganese nitrate solution at a rate of 0.5 mm / min for 4 minutes, and the immersion depth is 1 / 4 of the height of the anode tantalum block;
[0018] 4) Immerse the above anode tantalum block in the above manganese nitrate solution at a speed of 1.5 mm / min for 3 minutes;
[0019] 5) Take out the anode tantalum block from the manganese nitrate solution at a speed of 1.5 mm / min, and then put it into the decomposition furnace to prepare the manganese dioxide dielectric film according to the conventional method.
Embodiment 2
[0021] The steps are the same as in Example 1; wherein, the immersion speed in step 3) is 1.5 mm / min, the holding time is 2 minutes, the immersion depth is 1 / 5 of the height of the anode tantalum block, and the immersion speed in step 4) is 0.5 mm / min, the retention time is 5 minutes, and the removal speed in step 5) is 0.5mm / min.
Embodiment 3
[0023] The steps are the same as in Example 1; wherein, the immersion speed in step 3) is 1 mm / min, the holding time is 3 minutes, the immersion depth is 1 / 5 of the height of the anode tantalum block, and the immersion speed in step 4) is 1 mm / min, the retention time is 4 minutes, and the removal speed in step 5) is 1mm / min.
[0024] In above-mentioned each embodiment, each technical parameter of described manganese nitrate solution is all identical with the manganese nitrate solution that traditional common method adopts.
PUM
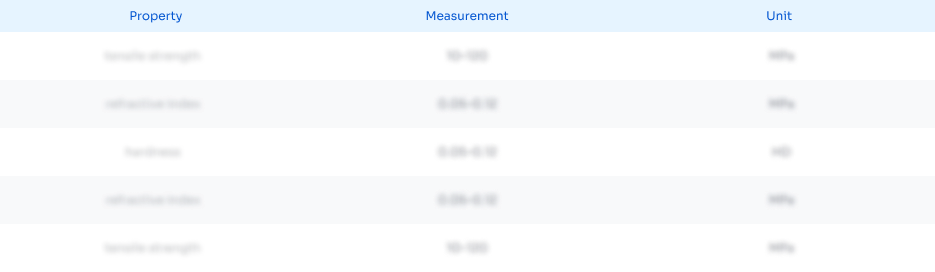
Abstract
Description
Claims
Application Information

- R&D
- Intellectual Property
- Life Sciences
- Materials
- Tech Scout
- Unparalleled Data Quality
- Higher Quality Content
- 60% Fewer Hallucinations
Browse by: Latest US Patents, China's latest patents, Technical Efficacy Thesaurus, Application Domain, Technology Topic, Popular Technical Reports.
© 2025 PatSnap. All rights reserved.Legal|Privacy policy|Modern Slavery Act Transparency Statement|Sitemap|About US| Contact US: help@patsnap.com