Vehicle driving apparatus
A driving device and vehicle technology, applied to power devices, pneumatic power devices, vehicle components, etc., can solve problems such as increased loads, and achieve the effect of suppressing changes in rotational speed and suppressing discomfort
- Summary
- Abstract
- Description
- Claims
- Application Information
AI Technical Summary
Problems solved by technology
Method used
Image
Examples
no. 1 approach
[0038] A first embodiment of a vehicle drive device according to the present invention will be described with reference to the drawings. Such as figure 1 As shown, the vehicle drive device 1 according to the present embodiment is a drive device (hybrid vehicle drive device) for driving a vehicle (hybrid vehicle) provided with an internal combustion engine E and rotary electric machines MG1 and MG2 as drive force sources for wheels W. drive unit). Furthermore, the vehicle drive device 1 according to the present embodiment includes a control device 70 (see image 3 ), the control device 70 is based on image 3 The system configuration shown is used to control the operation of each driving force source and the like. Among them, in image 3 In , the dotted line indicates the transmission path of electric power, and the solid line arrow indicates the transmission path of various information.
[0039] Such as figure 1 As shown, in the present embodiment, the differential gear ...
no. 2 approach
[0124] A second embodiment of the vehicle drive system according to the present invention will be described with reference to the drawings. The vehicle drive device 1 according to the present embodiment differs from the configuration of the above-described first embodiment mainly in the method of determining the completion of the axis center adjustment by the centering control unit 77 and the configuration related thereto. Hereinafter, the configuration of the vehicle drive device 1 according to the present embodiment will be described focusing on differences from the first embodiment described above. However, points not particularly described are the same as those of the first embodiment described above.
[0125] The centering control unit 77 performs the completion determination of the axis center adjustment based on the rotational speed difference ΔN between the input member I and the intermediate member M, at least as in the first embodiment described above. In the presen...
PUM
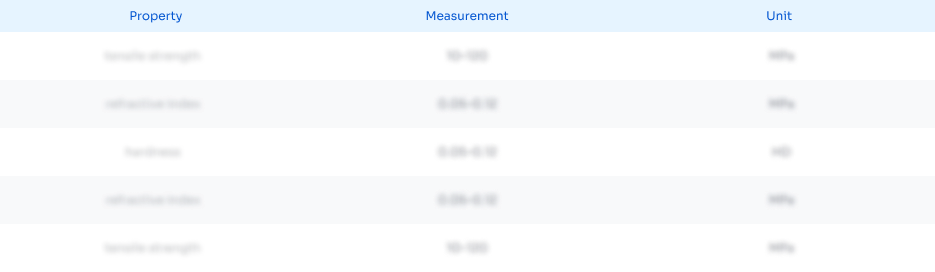
Abstract
Description
Claims
Application Information

- R&D Engineer
- R&D Manager
- IP Professional
- Industry Leading Data Capabilities
- Powerful AI technology
- Patent DNA Extraction
Browse by: Latest US Patents, China's latest patents, Technical Efficacy Thesaurus, Application Domain, Technology Topic, Popular Technical Reports.
© 2024 PatSnap. All rights reserved.Legal|Privacy policy|Modern Slavery Act Transparency Statement|Sitemap|About US| Contact US: help@patsnap.com