Pressurization control method and pressurization control system for rotary drilling rig
A technology of rotary drilling rig and control system, which is applied to the automatic control system of drilling, drilling equipment, earthwork drilling and mining, etc. It can solve problems such as open welding of the square head, damage of structural parts, and drop of the drill bit, so as to avoid operation delay , the effect of reducing the vibration frequency
- Summary
- Abstract
- Description
- Claims
- Application Information
AI Technical Summary
Problems solved by technology
Method used
Image
Examples
Embodiment Construction
[0027] Specific embodiments of the present invention will be described in detail below in conjunction with the accompanying drawings. It should be understood that the specific embodiments described here are only used to illustrate and explain the present invention, and are not intended to limit the present invention.
[0028] In the present invention, unless otherwise specified, the used orientation words such as "upper and lower" are words used to describe the mutual positional relationship between the various components of the rotary drilling rig under normal working conditions.
[0029] Generally, a rotary drilling rig includes a mast 10, a left mast oil cylinder 11, a right mast oil cylinder 16, a drill pipe 50, a main winch (not shown) for controlling the rise or fall of the drill pipe 50, and a traveling frame connected with the drill pipe 50. 30 and power head 40, pressurized oil cylinder 20 for power head 40 pressurization, and parts such as drill bit 60. For the work...
PUM
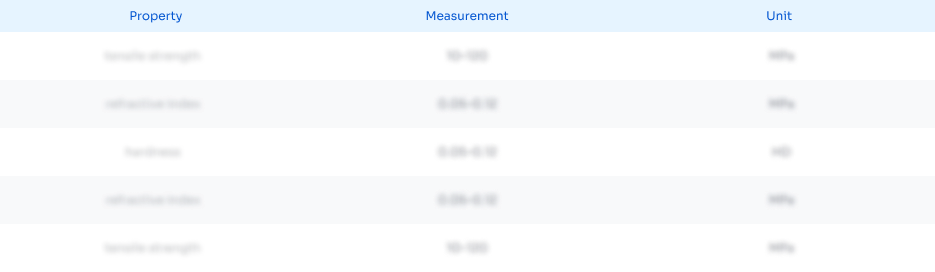
Abstract
Description
Claims
Application Information

- R&D
- Intellectual Property
- Life Sciences
- Materials
- Tech Scout
- Unparalleled Data Quality
- Higher Quality Content
- 60% Fewer Hallucinations
Browse by: Latest US Patents, China's latest patents, Technical Efficacy Thesaurus, Application Domain, Technology Topic, Popular Technical Reports.
© 2025 PatSnap. All rights reserved.Legal|Privacy policy|Modern Slavery Act Transparency Statement|Sitemap|About US| Contact US: help@patsnap.com