Method for preparing multi-component composite fibers
A composite fiber and multi-component technology, applied in fiber processing, fiber chemical characteristics, rayon manufacturing, etc., can solve problems such as lack of intellectual property rights
- Summary
- Abstract
- Description
- Claims
- Application Information
AI Technical Summary
Problems solved by technology
Method used
Image
Examples
Embodiment 1
[0062] 1) if figure 1 , The present invention adopts such process steps: slice selection and drying→screw extruder→filter→spinning box→metering pump→composite spinning assembly→side blowing cooling device→gode roll→coiler. The raw materials are polyester chips, polyamide and polypropylene with similar spinning temperature, and are dried by vacuum drying system. The drying temperature is generally 160°C-170°C, and the drying time is 7-8 hours. The control of silk temperature is shown in Table 1. The cooling process uses a side blowing device for cooling. The wind pressure of this device is ≥0.45m / s, the relative humidity is 65%RH±2%RH, the wind temperature is 25°C±0.5°C, and the wind speed The air outlet is 0.5m / s, and the distance between the air outlet and the plate surface is 150mm. Finally, it is wound into a tube by a high-speed winding machine with a winding speed of 3010m / min.
[0063] 2) if Figures 2 to 5 As shown, a spinning pack for producing three-component paral...
Embodiment 2
[0075] 1) if figure 1 , The present invention adopts such process steps: slice selection and drying→screw extruder→filter→spinning box→metering pump→composite spinning assembly→side blowing cooling device→gode roll→coiler. The raw materials are polyester chips, polyamide and polypropylene with similar spinning temperature, and are dried by vacuum drying system. The drying temperature is generally 160°C-170°C, and the drying time is 7-8 hours. The control of silk temperature is shown in Table 1. The cooling process uses a side blowing device for cooling. The wind pressure of this device is ≥0.45m / s, the relative humidity is 65%RH±2%RH, the wind temperature is 25°C±0.5°C, and the wind speed The air outlet is 0.5m / s, and the distance between the air outlet and the plate surface is 150mm. Finally, it is wound into a tube by a high-speed winding machine with a winding speed of 3010m / min.
[0076] 2) if Figures 7 to 10 As shown, a spinning assembly for producing three-component ...
PUM
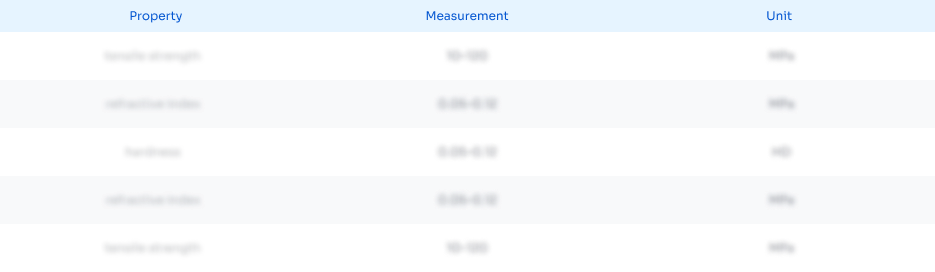
Abstract
Description
Claims
Application Information

- R&D
- Intellectual Property
- Life Sciences
- Materials
- Tech Scout
- Unparalleled Data Quality
- Higher Quality Content
- 60% Fewer Hallucinations
Browse by: Latest US Patents, China's latest patents, Technical Efficacy Thesaurus, Application Domain, Technology Topic, Popular Technical Reports.
© 2025 PatSnap. All rights reserved.Legal|Privacy policy|Modern Slavery Act Transparency Statement|Sitemap|About US| Contact US: help@patsnap.com