Silk screen printing ink for metal
A screen and ink technology, applied in the field of ink, can solve the problems of high energy consumption, poor adhesion and light resistance, low ink production efficiency, etc., to achieve low energy consumption, reduce labor intensity, and high production efficiency. Effect
- Summary
- Abstract
- Description
- Claims
- Application Information
AI Technical Summary
Problems solved by technology
Method used
Examples
Embodiment 1
[0009] This embodiment provides a screen ink for metal, which contains the following components in parts by mass: 25 parts by mass of colloidal calcium carbonate, 10 parts by mass of ethylene glycol butyl ether, 15 parts by mass of kelvin, 35 parts by mass of titanium dioxide, flax 50 parts by mass of oil alkyd resin, 10 parts by mass of precipitated barium sulfate, 15 parts by mass of butanol etherified melamine resin, 15 parts by mass of paraffin wax, 15 parts by mass of white beet oil, 30 parts by mass of dehydrated castor oil alkyd resin, n-butanol 1 part by mass.
Embodiment 2
[0011] The present embodiment provides a screen ink for metal, which contains the following components in parts by mass: 30 parts by mass of colloidal calcium carbonate, 20 parts by mass of ethylene glycol butyl ether, 30 parts by mass of kaolin, 40 parts by mass of titanium dioxide, flax 60 parts by mass of oil alkyd resin, 15 parts by mass of precipitated barium sulfate, 20 parts by mass of butanol etherified melamine resin, 20 parts by mass of paraffin wax, 20 parts by mass of white beet oil, 40 parts by mass of dehydrated castor oil alkyd resin, n-butanol 2 parts by mass.
Embodiment 3
[0013] The present embodiment provides a screen ink for metal, which contains the following components in parts by mass: 27 parts by mass of colloidal calcium carbonate, 15 parts by mass of ethylene glycol butyl ether, 20 parts by mass of kelvin, 38 parts by mass of titanium dioxide, flax 55 parts by mass of oil alkyd resin, 12.5 parts by mass of precipitated barium sulfate, 17 parts by mass of butanol etherified melamine resin, 18 parts by mass of paraffin, 17 parts by mass of white beet oil, 35 parts by mass of dehydrated castor oil alkyd resin, n-butanol 1.5 parts by mass.
PUM
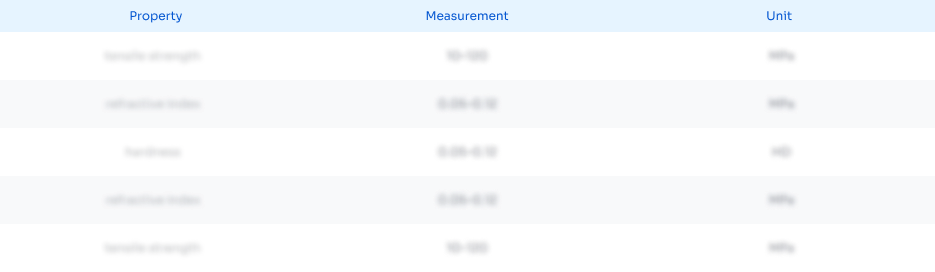
Abstract
Description
Claims
Application Information

- Generate Ideas
- Intellectual Property
- Life Sciences
- Materials
- Tech Scout
- Unparalleled Data Quality
- Higher Quality Content
- 60% Fewer Hallucinations
Browse by: Latest US Patents, China's latest patents, Technical Efficacy Thesaurus, Application Domain, Technology Topic, Popular Technical Reports.
© 2025 PatSnap. All rights reserved.Legal|Privacy policy|Modern Slavery Act Transparency Statement|Sitemap|About US| Contact US: help@patsnap.com