Carbon felt conductivity test method
A test method and conductivity technology, which is applied in the field of conductivity testing of carbon felt, can solve the problems of large error, uneven conductivity of carbon fiber, large dispersion of results, etc., to achieve small error, easy testing, and small dispersion Effect
- Summary
- Abstract
- Description
- Claims
- Application Information
AI Technical Summary
Problems solved by technology
Method used
Image
Examples
specific Embodiment example 1
[0019] Use oil bath heating to reach 300°C to heat solid sulfur to form liquid sulfur, usually the heating temperature requirement can be met;
[0020] Cutting and forming a soft and easily deformable carbon felt with a cross-sectional area S of 10mmX10mm and a length L of 100mm in the shape of a three-dimensional rectangular strip using directly purchased carbon felt, completely soaking the carbon felt into the liquid sulfur, and then taking it out and soaking it completely carbon felt to form impregnated carbon felt;
[0021] The impregnated carbon felt is taken out from the liquid sulfur and placed at room temperature, and the impregnated carbon felt is left to cool, and the liquid sulfur absorbed in the impregnated carbon felt is cooled and solidified, and the impregnated carbon felt is also Subsequently, the cooling shape is fixed, forming a solid carbon felt with a fixed shape with the cross-sectional area S being 10mm×10mm and the length L being 100mm;
[0022] Put the...
specific Embodiment example 2
[0025] Use oil bath heating to reach 315°C to heat solid sulfur to form liquid sulfur, and the usual conditions can meet the heating temperature requirements;
[0026] Cutting and forming a soft and easily deformable carbon felt with a cross-sectional area S of 10mmX10mm and a length L of 100mm in the shape of a three-dimensional rectangular strip using directly purchased carbon felt, completely soaking the carbon felt into the liquid sulfur, and then taking it out and soaking it completely carbon felt to form impregnated carbon felt;
[0027] The impregnated carbon felt is taken out from the liquid sulfur and placed at room temperature, and the impregnated carbon felt is left to cool, and the liquid sulfur absorbed in the impregnated carbon felt is cooled and solidified, and the impregnated carbon felt is also Subsequently, the cooling shape is fixed, forming a solid carbon felt with a fixed shape with the cross-sectional area S being 10mm×10mm and the length L being 100mm; ...
specific Embodiment example 3
[0031] Oil bath heating is used to reach 330°C to heat solid sulfur to form liquid sulfur, and the heating temperature requirements can be met under normal conditions;
[0032] Cutting and forming a soft and easily deformable carbon felt with a cross-sectional area S of 10mmX10mm and a length L of 100mm in the shape of a three-dimensional rectangular strip using directly purchased carbon felt, completely soaking the carbon felt into the liquid sulfur, and then taking it out and soaking it completely carbon felt to form impregnated carbon felt;
[0033] The impregnated carbon felt is taken out from the liquid sulfur and placed at room temperature, and the impregnated carbon felt is left to cool, and the liquid sulfur absorbed in the impregnated carbon felt is cooled and solidified, and the impregnated carbon felt is also Subsequently, the cooling shape is fixed, forming a solid carbon felt with a fixed shape with the cross-sectional area S being 10mm×10mm and the length L being...
PUM
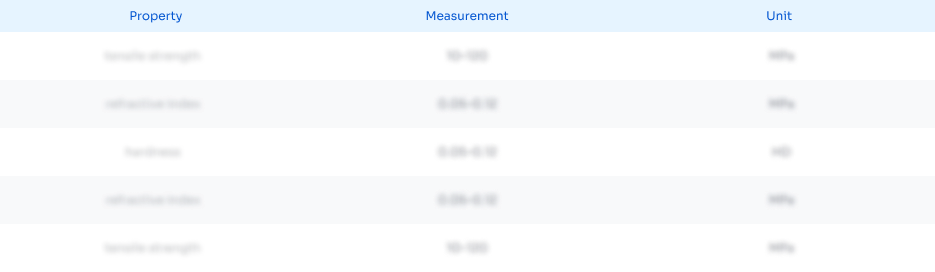
Abstract
Description
Claims
Application Information

- R&D
- Intellectual Property
- Life Sciences
- Materials
- Tech Scout
- Unparalleled Data Quality
- Higher Quality Content
- 60% Fewer Hallucinations
Browse by: Latest US Patents, China's latest patents, Technical Efficacy Thesaurus, Application Domain, Technology Topic, Popular Technical Reports.
© 2025 PatSnap. All rights reserved.Legal|Privacy policy|Modern Slavery Act Transparency Statement|Sitemap|About US| Contact US: help@patsnap.com