Flame resistant plastic and preparation method thereof
A technology of flame retardant plastics and flame retardants, applied in the field of organic polymer composite materials, can solve the problems of human suffocation, side effects, damage to physical and mental health, etc., to improve market competitiveness and solve the effect of insufficient flame retardant performance
- Summary
- Abstract
- Description
- Claims
- Application Information
AI Technical Summary
Problems solved by technology
Method used
Image
Examples
Embodiment 1
[0032] According to the formula quantity, weigh each component, and mix uniformly; put the material obtained by mixing uniformly into a parallel twin-screw extruder, and the barrel temperature of the parallel twin-screw extruder is 70°C to obtain an extruded material; The discharged material is fed into a single-screw granulator, and its temperature is 90°C.
Embodiment 2
[0034] According to the formula amount, weigh each component, and mix uniformly; put the material obtained by mixing uniformly into a parallel twin-screw extruder, and the barrel temperature of the parallel twin-screw extruder is 90°C to obtain an extruded material; The discharged material is fed into a single-screw granulator, and its temperature is 110° C. to obtain the final product.
Embodiment 3
[0036] According to the formula amount, weigh each component, and mix uniformly; put the material obtained by mixing uniformly into a parallel twin-screw extruder, and the barrel temperature of the parallel twin-screw extruder is 80°C to obtain an extruded material; The discharged material is fed into a single-screw granulator at a temperature of 100°C to obtain the product.
PUM
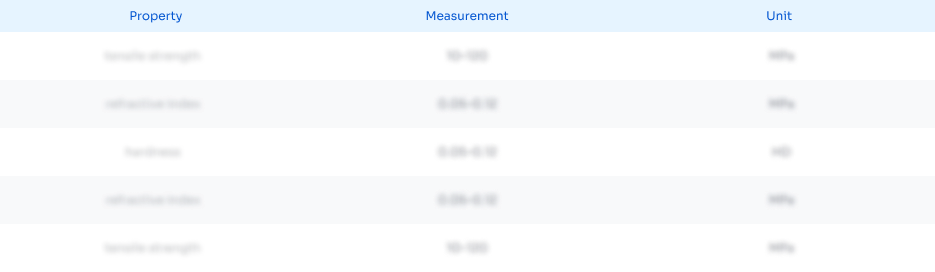
Abstract
Description
Claims
Application Information

- R&D Engineer
- R&D Manager
- IP Professional
- Industry Leading Data Capabilities
- Powerful AI technology
- Patent DNA Extraction
Browse by: Latest US Patents, China's latest patents, Technical Efficacy Thesaurus, Application Domain, Technology Topic, Popular Technical Reports.
© 2024 PatSnap. All rights reserved.Legal|Privacy policy|Modern Slavery Act Transparency Statement|Sitemap|About US| Contact US: help@patsnap.com