Temperature control system
A technology of temperature control system and temperature controller, which is applied in the direction of temperature control using electric methods, and can solve problems such as high performance requirements and poor anti-interference ability
- Summary
- Abstract
- Description
- Claims
- Application Information
AI Technical Summary
Problems solved by technology
Method used
Image
Examples
Embodiment Construction
[0031] refer to figure 1, temperature control system, including multiple distributed heat sources and multiple temperature sensors, the heat sources correspond to the temperature sensors one by one, each heat source is connected to its own power drive module, all power drive modules are controlled by the temperature controller, the temperature The controller takes the target temperature as a reference input and the output temperature of each temperature sensor as a feedback.
[0032] The tracking error between the reference input and output temperature is input into the temperature controller, and the temperature controller converts the tracking error into an average error, and calculates the average control amount and the error deviation between the tracking error and the average error based on the average error, and then according to The error deviation obtains the superposition control quantity of each heat source, and the sum signal of the average control quantity and the ...
PUM
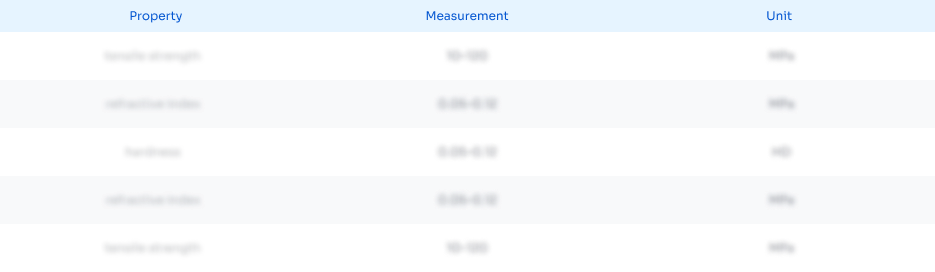
Abstract
Description
Claims
Application Information

- R&D
- Intellectual Property
- Life Sciences
- Materials
- Tech Scout
- Unparalleled Data Quality
- Higher Quality Content
- 60% Fewer Hallucinations
Browse by: Latest US Patents, China's latest patents, Technical Efficacy Thesaurus, Application Domain, Technology Topic, Popular Technical Reports.
© 2025 PatSnap. All rights reserved.Legal|Privacy policy|Modern Slavery Act Transparency Statement|Sitemap|About US| Contact US: help@patsnap.com