Turnover machine
A technology of turning machine and frame, which is applied in the field of turning machines, which can solve the problems of long installation period, high ground requirements, and many power equipment, and achieve the effect of reducing the working height
- Summary
- Abstract
- Description
- Claims
- Application Information
AI Technical Summary
Problems solved by technology
Method used
Image
Examples
Embodiment Construction
[0020] Such as Figure 3 to Figure 7 Shown, the turnover machine of low working height of the present invention, this turnover machine comprises frame 1, rotating mechanism 2, moving mechanism 3 and at least four sets of fork bars 4, and turning mechanism 2 and moving mechanism 3 are all horizontally installed on the machine. On the frame 1, when the plate held by the two-fork lever 4 from the plate-feeding position, after the rotating mechanism 2 rotates 180°, the two-fork lever 4 is driven by the moving mechanism 3, and is pushed back to the original plate-feeding position, reaching the two-fork, 4. The purpose of circularly clamping the sheet material and turning over, because the fork bar 4 only rotates in the upper half of the turning machine, reduces the working height of the turning machine.
[0021] The rotating mechanism 2 of the described turning machine comprises a rotating drive device 21, at least two rotating disks 22, a rotating shaft 23 and a plurality of group...
PUM
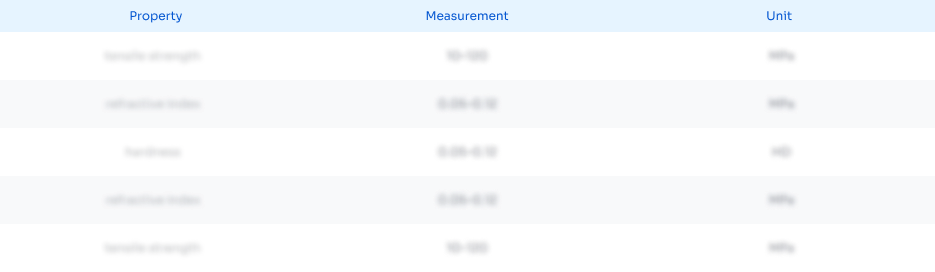
Abstract
Description
Claims
Application Information

- R&D
- Intellectual Property
- Life Sciences
- Materials
- Tech Scout
- Unparalleled Data Quality
- Higher Quality Content
- 60% Fewer Hallucinations
Browse by: Latest US Patents, China's latest patents, Technical Efficacy Thesaurus, Application Domain, Technology Topic, Popular Technical Reports.
© 2025 PatSnap. All rights reserved.Legal|Privacy policy|Modern Slavery Act Transparency Statement|Sitemap|About US| Contact US: help@patsnap.com