Method for designing composite material beam for helicopter and fixed-wing aircraft
A composite material and design method technology, applied in the field of composite material beam design and section structure design, can solve the problems of small design space, complex beam structure design, difficult to meet rigid body characteristics and shear center position, etc., to improve performance and improve performance. Effect
- Summary
- Abstract
- Description
- Claims
- Application Information
AI Technical Summary
Problems solved by technology
Method used
Image
Examples
Embodiment
[0087] In order to verify the composite material beam design method proposed in the present invention, the topological structures of the fixed-wing aircraft wing sections with square section and NACA0018 section shapes are designed respectively. The square section consists of 25×25 grids, each with 9 types of materials. One isotropic material and one anisotropic material are included, and the anisotropic material considers two fiber plane directions and four fiber directions, so there are eight candidate anisotropic material types. The material properties of the two materials are shown in Table 1:
[0088] Table 1 Material properties
[0089]
[0090] The length of the square section beam is 80mm, and the end shear force is loaded. The fibers and fiber plane directions in the final topological structure of the section are as follows: Figure 6 and Figure 7 shown. A blank cell indicates that the cell is mainly composed of isotropic materials, while the length and angle ...
PUM
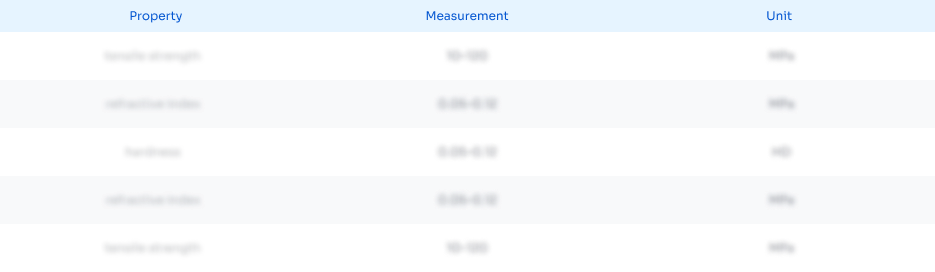
Abstract
Description
Claims
Application Information

- Generate Ideas
- Intellectual Property
- Life Sciences
- Materials
- Tech Scout
- Unparalleled Data Quality
- Higher Quality Content
- 60% Fewer Hallucinations
Browse by: Latest US Patents, China's latest patents, Technical Efficacy Thesaurus, Application Domain, Technology Topic, Popular Technical Reports.
© 2025 PatSnap. All rights reserved.Legal|Privacy policy|Modern Slavery Act Transparency Statement|Sitemap|About US| Contact US: help@patsnap.com