Machining method of profiling lower die blank of 22224 aligning spherical roller
A technology of spherical rollers, processing methods, applied in the field of bearing parts manufacturing
- Summary
- Abstract
- Description
- Claims
- Application Information
AI Technical Summary
Problems solved by technology
Method used
Image
Examples
Embodiment Construction
[0012] A method for processing a 22224 self-aligning spherical roller die blank, comprising the following process steps:
[0013] (1) Cutting material: select Gr15 high-carbon chromium steel, forging blanking, material diameter Φ120, cutting length 175, waiting for forging and casting;
[0014] (2) The starting temperature of forging is 1130°C. After upsetting the forging material, forge the square, draw the square to length, then upset, forge the square, draw the square to length, then upset, forge the square, and draw the square to length , followed by three times in succession to form the tire, stop the forging temperature at 800°C, and punch out a cavity with a processing capacity of 2 mm on the end face of the die, so that the metal fiber direction of the material is in line with the force axis of the lower die. The direction is vertical, and the fiber direction of the surrounding material of the cavity is perpendicular to the force direction of the press type, that is to...
PUM
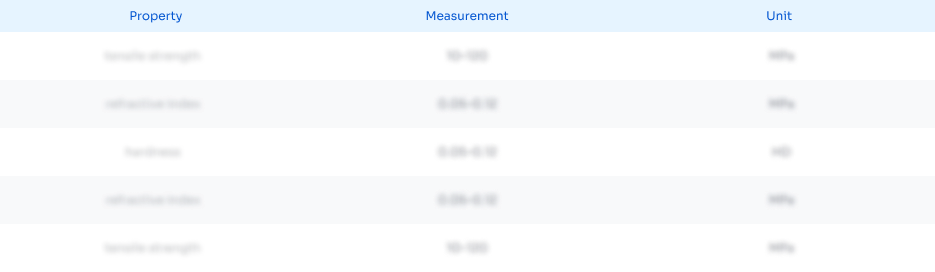
Abstract
Description
Claims
Application Information

- R&D
- Intellectual Property
- Life Sciences
- Materials
- Tech Scout
- Unparalleled Data Quality
- Higher Quality Content
- 60% Fewer Hallucinations
Browse by: Latest US Patents, China's latest patents, Technical Efficacy Thesaurus, Application Domain, Technology Topic, Popular Technical Reports.
© 2025 PatSnap. All rights reserved.Legal|Privacy policy|Modern Slavery Act Transparency Statement|Sitemap|About US| Contact US: help@patsnap.com