Six-freedom-degree decoupling modeling method of workpiece platform micro-motion part
A modeling method and workpiece table technology are applied in the field of ultra-precision manufacturing to achieve the effect of ensuring motion accuracy and improving exposure quality
- Summary
- Abstract
- Description
- Claims
- Application Information
AI Technical Summary
Problems solved by technology
Method used
Image
Examples
specific Embodiment approach 1
[0017] Specific implementation mode 1: The six-degree-of-freedom decoupling modeling method of the micro-movement part of the workpiece table in this implementation mode is implemented according to the following steps:
[0018] 1. According to the installation position and angle of the voice coil motor, establish the conversion relationship between the center-of-mass driving force and torque of the micro-movement part of the workpiece table and the driving force of the voice coil motor;
[0019] 2. Establish the positional relationship between the exposure center and the center of mass of the micro-movement part of the workpiece table;
[0020] 3. Secondary derivation of the positional relationship obtained in step 2 and ignoring the primary differential item to obtain the acceleration relationship between the center of mass of the micro-moving part of the workpiece table and the exposure center;
[0021] 4. According to Newton's second law, the relationship between the drivin...
specific Embodiment approach 2
[0027] Specific embodiment 2: The difference between this embodiment and specific embodiment 1 is that in step 1, the conversion relationship between the driving force and torque of the center of mass of the micro-movement part of the workpiece table and the driving force of the voice coil motor is specifically: F cog =L·f
[0028] where the matrix F cog =[F xcog f ycog T zcog f zcog T xcog T ycog ] T ,
[0029] f=[f 1 f 2 f 3 f 4 f 5 f 6 ] T ,
[0030] L = - cos θ 1 - cos θ 2 cos θ 3 0 0 ...
specific Embodiment approach 3
[0032] Embodiment 3: The difference between this embodiment and Embodiment 1 or 2 is that in Step 2, the positional relationship between the exposure center and the center of mass of the micro-movement part of the workpiece table is specifically:
[0033] x cog = x - ( y + y 0 ) r z + ( z + z 0 ) r y y cog ...
PUM
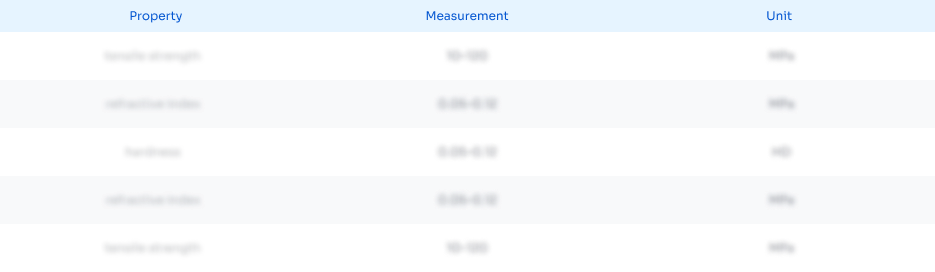
Abstract
Description
Claims
Application Information

- R&D
- Intellectual Property
- Life Sciences
- Materials
- Tech Scout
- Unparalleled Data Quality
- Higher Quality Content
- 60% Fewer Hallucinations
Browse by: Latest US Patents, China's latest patents, Technical Efficacy Thesaurus, Application Domain, Technology Topic, Popular Technical Reports.
© 2025 PatSnap. All rights reserved.Legal|Privacy policy|Modern Slavery Act Transparency Statement|Sitemap|About US| Contact US: help@patsnap.com