Work control system of anchor and mooring machines
A work control and anchor winch technology, applied in the direction of the clockwork mechanism, hoisting device, etc., can solve the problems of complex composition, high cost, low reliability, etc., and achieve low cost, high reliability, and simple system composition. Effect
- Summary
- Abstract
- Description
- Claims
- Application Information
AI Technical Summary
Problems solved by technology
Method used
Image
Examples
Embodiment 1
[0025] refer to figure 1 In this embodiment, the working control system of the windlass windlass includes a servo pump station PS and a plurality of first direction switching valves. Each first direction switching valve corresponds to a winch or windlass. Specific instructions are given below.
[0026] Corresponding to the first direction switching valve 210 of windlass W1, its first oil port 211 and second oil port 212 are connected to the oil outlet of the servo pump station PS, and the third oil port 213 and fourth oil port 214 are connected to the servo pump station The oil return port of PS, the fifth oil port 215 is connected to the first oil port 811 of the first controller 810 and the first oil port 821 of the second controller 820 on the motor of the windlass W1, and the sixth oil port 216 is connected to the anchor The second oil port 812 of the first controller 810 and the second oil port 822 of the second controller 820 on the motor of machine W1.
[0027] The w...
Embodiment 2
[0036] refer to figure 2 In this embodiment, the working control system of the windlass windlass includes a servo pump station PS, five first direction switching valves, multiple second direction switching valves and multiple authority selection valve groups. The connection relationship and working principle of the servo pump station PS and the first direction switching valve are similar to the fifth embodiment above, the difference is that each second direction switching valve group and each authority selection valve group correspond to a winch or anchor machine.
[0037] Corresponding to the second direction switching valve 310 of windlass W1, the first oil port 311 and the second oil port 312 are connected to the oil outlet of the servo pump station PS, and the third oil port 313 and the fourth oil port 314 are connected to the servo pump station The oil return port of PS corresponds to the authority selection valve group of windlass W1, which includes a two-position six-...
Embodiment 3
[0049] refer to image 3 , the work control system of the anchor winch in this embodiment includes a servo pump station PS, 5 first direction switching valves, 5 second direction switching valves and 5 authority selection valve groups, and each authority selection valve group includes a two-position six-way reversing valve. Among them, the connection relationship and working principle of the servo pump station PS, the first direction switching valve, the second direction switching valve, and the two-position six-way switching valve are similar to those in the sixth embodiment above. The difference is that each authority selection valve group also includes The first sequence valve 902 , the first one-way valve 901 , the second sequence valve 904 and the second one-way valve 903 .
[0050] Fig. 7a is an enlarged schematic diagram of part M of the authority selection valve group provided by the embodiment shown in Fig. 7 . Referring to Figure 7a and in combination with Figure 7...
PUM
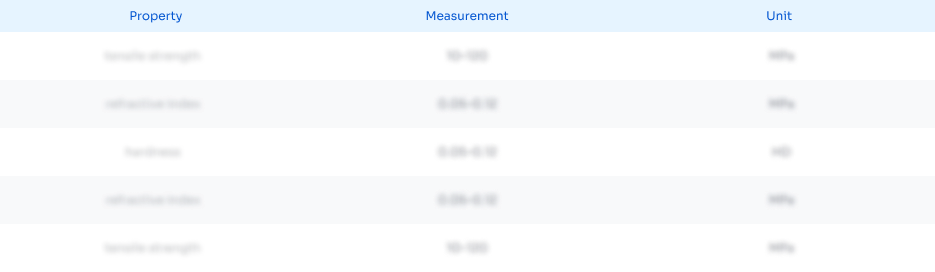
Abstract
Description
Claims
Application Information

- R&D
- Intellectual Property
- Life Sciences
- Materials
- Tech Scout
- Unparalleled Data Quality
- Higher Quality Content
- 60% Fewer Hallucinations
Browse by: Latest US Patents, China's latest patents, Technical Efficacy Thesaurus, Application Domain, Technology Topic, Popular Technical Reports.
© 2025 PatSnap. All rights reserved.Legal|Privacy policy|Modern Slavery Act Transparency Statement|Sitemap|About US| Contact US: help@patsnap.com