Area array infrared camera quick scaling and heterogeneity calibrating method based on variant integral time
A non-uniformity correction, infrared camera technology, applied in radiation pyrometry, measuring devices, instruments, etc., can solve the problem of not considering IRFPA blind element detection and compensation, not getting rid of black body dependence, and least squares integration time points are many, etc. question
- Summary
- Abstract
- Description
- Claims
- Application Information
AI Technical Summary
Problems solved by technology
Method used
Image
Examples
Embodiment Construction
[0037] The present invention is a non-uniformity correction method of area array infrared camera based on variable integration time calibration. Under the condition of fixed incident radiation, through FPGA software programming, the integration time of area array infrared camera is automatically increased at equal intervals, and 1 Increment to t n , And collect a frame of image under the corresponding integration time, set as X 1 (i, j), X 2 (i, j),......X n (i, j), the corresponding integration time is t 1 , T n ,...T n , (I, j) is the pixel coordinates; according to the classic two-point correction coefficient calculation formula, the correction coefficient G is calculated using two frames of images adjacent to the integration time k (i, j) and B k (i, j), k=1, 2,...n-1. The final gain correction coefficient G(i, j) is given by G k The weighted average value of (i, j) is obtained, and the offset correction coefficient B(i, j) is obtained by B k The mean value of (i, j) is obtain...
PUM
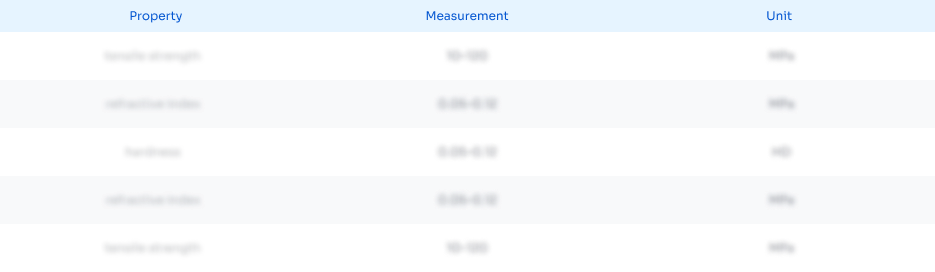
Abstract
Description
Claims
Application Information

- R&D Engineer
- R&D Manager
- IP Professional
- Industry Leading Data Capabilities
- Powerful AI technology
- Patent DNA Extraction
Browse by: Latest US Patents, China's latest patents, Technical Efficacy Thesaurus, Application Domain, Technology Topic, Popular Technical Reports.
© 2024 PatSnap. All rights reserved.Legal|Privacy policy|Modern Slavery Act Transparency Statement|Sitemap|About US| Contact US: help@patsnap.com