Method for preparing methanol by sensible heat of blast furnace slag
A blast furnace slag and methanol production technology, applied in blast furnace, blast furnace details, recycling technology and other directions, can solve the problems of high power consumption, reduced thermal energy quality, large energy consumption, etc., to improve energy efficiency, save energy, and eliminate carbon deposits. Effect
- Summary
- Abstract
- Description
- Claims
- Application Information
AI Technical Summary
Benefits of technology
Problems solved by technology
Method used
Image
Examples
Embodiment Construction
[0033] Below in conjunction with accompanying drawing, the present invention will be further described:
[0034] The present invention proposes a method for producing methanol by utilizing the sensible heat of blast furnace slag, which is characterized in that: the steps of the method are as follows:
[0035] (1) The blast furnace slag enters the sensible heat recovery device;
[0036] (2) The reactants enter the granulated slag packed bed to be preheated, and enter the granulated reactor after the temperature reaches 600°C;
[0037] (3) After the reactant enters the granulation reactor, it reacts at 850°C and 1 atmosphere to form methanol.
[0038] The heat required for the preheating and reaction of the above-mentioned reactants all comes from the sensible heat of blast furnace slag.
[0039] The reactions involved in the step (3) are the three-way reforming reaction of methane and the synthesis gas to methanol reaction.
[0040] The concrete reaction formula of described...
PUM
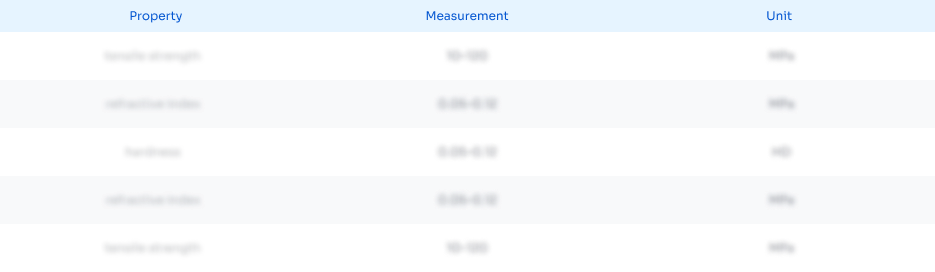
Abstract
Description
Claims
Application Information

- R&D Engineer
- R&D Manager
- IP Professional
- Industry Leading Data Capabilities
- Powerful AI technology
- Patent DNA Extraction
Browse by: Latest US Patents, China's latest patents, Technical Efficacy Thesaurus, Application Domain, Technology Topic, Popular Technical Reports.
© 2024 PatSnap. All rights reserved.Legal|Privacy policy|Modern Slavery Act Transparency Statement|Sitemap|About US| Contact US: help@patsnap.com