Robot wrist joint
A robot wrist and joint technology, applied in the directions of manipulators, manufacturing tools, joints, etc., can solve problems such as insufficient stability, three degrees of freedom cannot intersect at one point, and reduce control accuracy, and achieve simplified dynamic models and control algorithms. , Eliminate the problem of motion control coupling, the effect of simple hardware system
- Summary
- Abstract
- Description
- Claims
- Application Information
AI Technical Summary
Problems solved by technology
Method used
Image
Examples
Embodiment Construction
[0014] The present invention will be further described in detail below in conjunction with the accompanying drawings and embodiments.
[0015] As shown in the figure, a robot wrist joint includes a spherical housing 1 and a spherical revolving body 2. The housing 1 is set on the revolving body 2, and the revolving body 2 is fixedly equipped with an X-direction control rod group and a Y-direction control rod group. Rod group, the X-direction control rod group includes two X-direction control rods 3 on the same straight line and opposite to each other, and the Y-direction control rod group includes two Y-direction control rods 4 on the same straight line and opposite to each other The housing 1 is provided with guide grooves 11 at positions corresponding to the X-direction control rod 3 and the Y-direction control rod 4, and the X-direction control rod 3 and the Y-direction control rod 4 are respectively screwed with the rotary body 2 and protrude out from it. The guide groove 1...
PUM
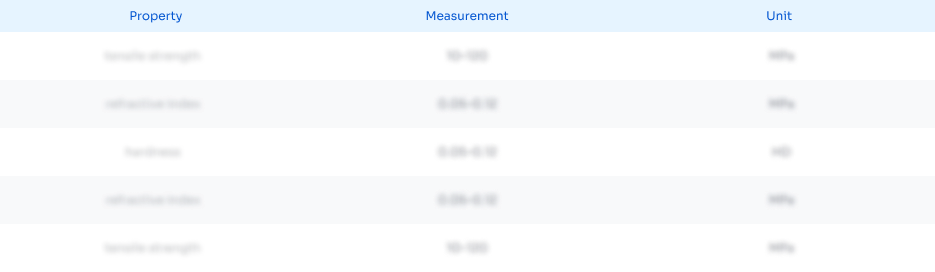
Abstract
Description
Claims
Application Information

- R&D Engineer
- R&D Manager
- IP Professional
- Industry Leading Data Capabilities
- Powerful AI technology
- Patent DNA Extraction
Browse by: Latest US Patents, China's latest patents, Technical Efficacy Thesaurus, Application Domain, Technology Topic, Popular Technical Reports.
© 2024 PatSnap. All rights reserved.Legal|Privacy policy|Modern Slavery Act Transparency Statement|Sitemap|About US| Contact US: help@patsnap.com