Cement clinker production technology for enriching CO2 by use of O2/CO2 combustion technology
A technology of cement clinker and combustion technology, which is applied in the field of cement clinker production process using O2/CO2 combustion technology to enrich CO2, which can solve the problems of large capture system, large energy consumption, and large volume, and achieve enhanced heat transfer , increase the radiation capacity, and promote the uniform temperature of the whole furnace
- Summary
- Abstract
- Description
- Claims
- Application Information
AI Technical Summary
Problems solved by technology
Method used
Image
Examples
Embodiment 1
[0027] Such as figure 2As shown, the raw meal entering the raw meal mill with a humidity of about 8% is heat-exchanged with the kiln tail gas at the outlet of the waste heat boiler. After the heat exchange, the raw meal is dried to a humidity of about 1%, and the temperature rises to 90-110°C , to homogenize the raw meal; the raw meal is transported to the five-stage cyclone preheater through the elevator, and the raw meal can be preheated to 700-800°C; the preheated raw meal powder is pre-decomposed in the calciner , into clinker at 850-950°C, which enters the rotary kiln through the feeding pipe, and then undergoes high-temperature forging in the rotary kiln to produce clinker at a temperature of 1200-1300°C, and then falls to the grate cooler through the rotary kiln mouth for cooling , Cool the clinker to about 90-100°C. The temperature of the flue gas at the kiln tail from the five-stage cyclone preheater is about 300-400°C. The exhaust gas waste heat power generation is...
Embodiment 2
[0031] The Egyptian raw meal was tested with a German Naisch STA409PC thermogravimetric analyzer. The initial temperature was 40°C, the end temperature was 1000°C, the heating rate was 20°C / min, and the mass of the raw meal was 10mg. Experiments show that (such as image 3 and Table 1): In the air atmosphere, the raw meal begins to decompose at 755°C, the decomposition rate reaches the maximum at 810°C, and ends at 831°C, the decomposition time is 3.8min, and the decomposition rate reaches 33.14%; when O 2 / CO 2 When the concentration is 40 / 60, the raw meal begins to decompose at 895°C, the decomposition rate reaches the maximum at 918°C, and ends at 941°C, the decomposition time is 2.3min, and the decomposition rate reaches 33.74%. 2 / CO 2 When the concentration is 30 / 70, the raw meal starts to decompose at 912°C, the decomposition rate reaches the maximum at 928°C, and ends at 954°C. The decomposition time is 2.1min, and the decomposition rate reaches 32.37%. 2 / CO 2 Whe...
PUM
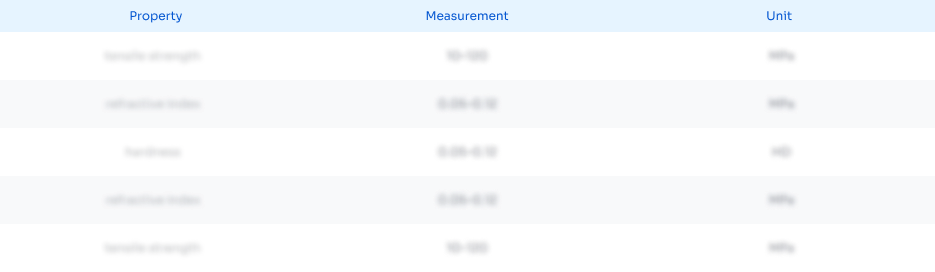
Abstract
Description
Claims
Application Information

- R&D Engineer
- R&D Manager
- IP Professional
- Industry Leading Data Capabilities
- Powerful AI technology
- Patent DNA Extraction
Browse by: Latest US Patents, China's latest patents, Technical Efficacy Thesaurus, Application Domain, Technology Topic, Popular Technical Reports.
© 2024 PatSnap. All rights reserved.Legal|Privacy policy|Modern Slavery Act Transparency Statement|Sitemap|About US| Contact US: help@patsnap.com