Mechanical filtering method of high-range acceleration sensor
An acceleration sensor, high-range technology, applied in the direction of measuring acceleration, speed/acceleration/shock measurement, instruments, etc., can solve the problems of complex manufacturing process, high production cost, and inability to meet the miniaturization requirements of high-range acceleration sensors, and achieve The effect of simplifying the manufacturing process and avoiding damage
- Summary
- Abstract
- Description
- Claims
- Application Information
AI Technical Summary
Problems solved by technology
Method used
Image
Examples
Embodiment Construction
[0015] A mechanical filtering method for a high-range acceleration sensor, which is implemented by the following steps:
[0016] a. Select the buffer layer 5 as the inner filter structure, and bond the sensitive structure 4 of the high-range acceleration sensor to the bottom surface of the inner chamber 3 of the tube shell 1 of the high-range acceleration sensor through the buffer layer 5; The sensitive structure 4 of the acceleration sensor performs filtering;
[0017] b. Select the mesa-shaped structure 6 as the outer filter structure, and ensure that the area of the upper bottom surface of the mesa-shaped structure 6 is greater than the area of the lower bottom surface of the tube shell 1 of the high-range acceleration sensor; then dig an arc cavity on the lower bottom surface of the mesa-shaped structure 6 7. Make the areas of the upper and lower bottom surfaces of the mesa-shaped structure 6 equal; then the shell 1 of the high-range acceleration sensor is fixed with t...
PUM
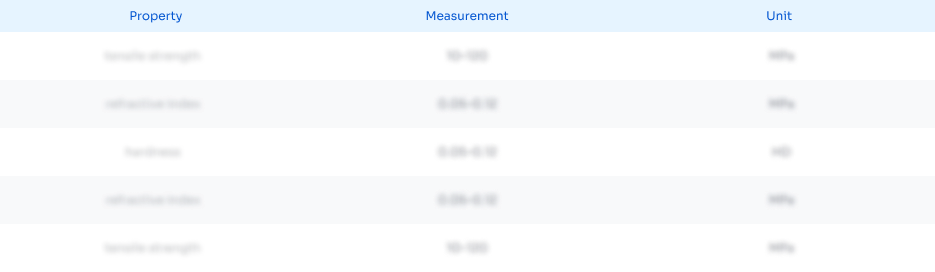
Abstract
Description
Claims
Application Information

- R&D Engineer
- R&D Manager
- IP Professional
- Industry Leading Data Capabilities
- Powerful AI technology
- Patent DNA Extraction
Browse by: Latest US Patents, China's latest patents, Technical Efficacy Thesaurus, Application Domain, Technology Topic, Popular Technical Reports.
© 2024 PatSnap. All rights reserved.Legal|Privacy policy|Modern Slavery Act Transparency Statement|Sitemap|About US| Contact US: help@patsnap.com