Method for separating bituminous substances from coal direct liquefaction residues
A technology of direct coal liquefaction and pitch, which is applied in the processing of tar pitch/petroleum pitch/natural pitch, the processing of tar pitch/petroleum pitch/natural pitch by selective extraction, and the petroleum industry, etc., which can solve the problem of high cost and low yield. and other problems to achieve the effect of reducing cost and improving extraction rate
- Summary
- Abstract
- Description
- Claims
- Application Information
AI Technical Summary
Problems solved by technology
Method used
Image
Examples
Embodiment approach
[0029] According to a typical implementation of the present invention, step S1 includes: S11, mixing the coal direct liquefaction residue and the extraction solvent according to a mass ratio of 1:1-10 to obtain a mixed solution; and S12, passing N into the mixed solution 2 or H 2 , and at 0.1-1.0MPa, heat the mixture to 50-280°C at 10°C-30°C / h, stir, extract, and heat-dissolve; the extraction time is 5-60min, and the stirring rate is 50-300r / min . In the present invention, the coal direct liquefaction residue and the extraction solvent are mixed according to a mass ratio of 1:1 to 10 to ensure the extraction effect and solvent recovery rate. If the mass ratio is higher than 1:1, the extraction solvent cannot completely liquefy the coal directly. The dissolution of asphalt substances in the residue leads to incomplete extraction; if the mass ratio is lower than 1:10, it will cause waste of extraction solvent and increase the recovery cost of subsequent extraction solvent. Inj...
Embodiment 1
[0037] 1) Add 250kg of coal direct liquefaction residue and 250kg of naphthalene oil (distillation range 120°C to 210°C) into the stirring tank, stir at a speed of 50r / min, and fill the stirring tank with N 2 After the pressure in the stirred tank reached 0.1 MPa, the temperature was raised to 50° C. at a rate of 10° C. per hour, stirred at a constant temperature, and subjected to hot-melt extraction for 30 minutes to obtain a hot-melt extraction mixture.
[0038] 2) Separation of solid and liquid from hot solution extraction mixture by means of hot pressure filtration. The primary filtration temperature is 150°C, the filtration pressure is 0.2MPa, and the pore size of the filter core is 50μm. After primary filtration, the primary extract and primary raffinate are collected. Part of the primary extract is sent to the secondary filter for hot-press filtration. The filtration temperature is 150°C, the filtration pressure is 0.15MPa, and the pore size of the filter element is 2 ...
Embodiment 2
[0042] 1) Add 250kg of coal direct liquefaction residue and 750kg of washing oil (distillation range 150-280°C) into the stirring tank, stir at a speed of 300r / min, and fill the stirring tank with N 2 After the pressure in the stirred tank reached 1.0 MPa, the temperature was raised to 280° C. at a rate of 30° C. per hour, stirred at a constant temperature, and hot-melted extraction was carried out for 60 minutes to obtain a hot-melted extraction mixture.
[0043] 2) Separation of solid and liquid from hot solution extraction mixture by means of hot pressure filtration. The primary filtration temperature is 120°C, the filtration pressure is 0.4MPa, and the pore size of the filter core is 40μm. After primary filtration, the primary extract and primary raffinate are collected. Part of the primary extract is sent to the secondary filter for hot-press filtration. The filtration temperature is 180°C, the filtration pressure is 0.3MPa, and the pore size of the filter element is 1 μ...
PUM
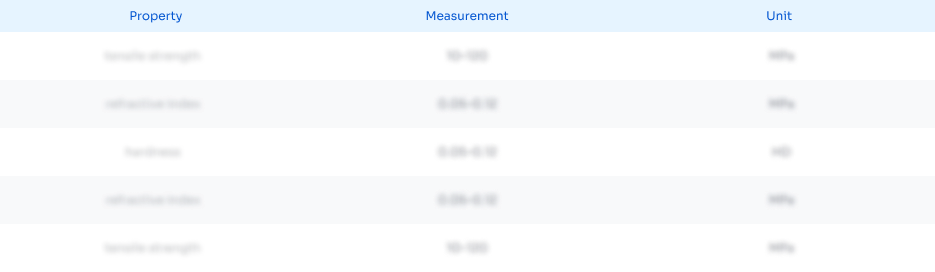
Abstract
Description
Claims
Application Information

- R&D
- Intellectual Property
- Life Sciences
- Materials
- Tech Scout
- Unparalleled Data Quality
- Higher Quality Content
- 60% Fewer Hallucinations
Browse by: Latest US Patents, China's latest patents, Technical Efficacy Thesaurus, Application Domain, Technology Topic, Popular Technical Reports.
© 2025 PatSnap. All rights reserved.Legal|Privacy policy|Modern Slavery Act Transparency Statement|Sitemap|About US| Contact US: help@patsnap.com