Linear electromagnetic damper with serially-connected magnetic circuit structure
A linear electromagnetic, series magnetic circuit technology, applied in the direction of magnetic springs, springs/shock absorbers, springs, etc., can solve the problem that the loading force cannot be continuously changed, and achieve the effect of eliminating the fluctuation of the loading force, high power density and low loss
- Summary
- Abstract
- Description
- Claims
- Application Information
AI Technical Summary
Problems solved by technology
Method used
Image
Examples
specific Embodiment approach 1
[0069] Specific implementation mode one: the following combination figure 1 Describe this embodiment mode, the linear electromagnetic damper of series magnetic circuit structure described in this embodiment mode, it comprises primary and secondary, is air gap between primary and secondary; Composed of 2n-1 primary permanent magnets 1-3, the air gap side surface of the primary iron core 1-1 is evenly opened with 2n-1 winding slots along the relative movement direction of the primary and secondary, so that the primary iron core 1-1 forms primary teeth A structure alternated with winding slots, the slotting direction of the winding slots is perpendicular to the relative movement direction of the primary and secondary, and n is a positive integer;
[0070] There is a coil wound on each primary tooth, the coils on the 1st, 3rd, 5th, ... and 2n-1 primary teeth are wound clockwise, and the coils on the 2nd, 4th, 6th, ... and 2n primary teeth The coil is wound counterclockwise, and ...
specific Embodiment approach 2
[0074] Specific implementation mode two: the following combination figure 2 Describe this embodiment, this embodiment will further explain Embodiment 1, the reaction plate 2-1 or the magnetic yoke plate 2-2 described in this embodiment are provided with parallel horizontal coolant channels;
[0075] The passage direction of the cooling liquid passage is parallel to the relative movement direction of the primary and secondary, and is evenly arranged along the slotting direction of the winding slots.
specific Embodiment approach 3
[0076] Specific implementation mode three: the following combination image 3 and Figure 4 Describe this embodiment, the linear electromagnetic damper with a series magnetic circuit structure described in this embodiment, the electromagnetic damper is a double-primary structure, the two primary mirrors are symmetrically arranged on both sides of the secondary, and the primary and secondary are air gap;
[0077] Each primary is composed of a primary iron core 1-1, an excitation winding 1-2 and 2n-1 primary permanent magnets 1-3, and the air gap side surface of the primary iron core 1-1 is evenly opened along the relative movement direction of the primary and secondary 2n-1 winding slots, so that the primary core 1-1 forms a structure in which the primary teeth and the winding slots alternate, the slotting direction of the winding slots is perpendicular to the relative movement direction of the primary and secondary, and n is a positive integer;
[0078] There is a coil wound...
PUM
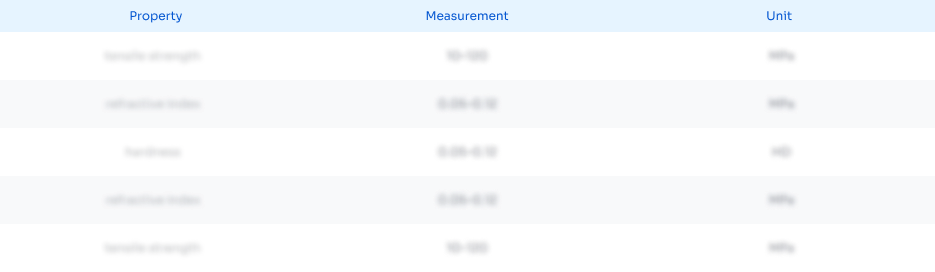
Abstract
Description
Claims
Application Information

- R&D
- Intellectual Property
- Life Sciences
- Materials
- Tech Scout
- Unparalleled Data Quality
- Higher Quality Content
- 60% Fewer Hallucinations
Browse by: Latest US Patents, China's latest patents, Technical Efficacy Thesaurus, Application Domain, Technology Topic, Popular Technical Reports.
© 2025 PatSnap. All rights reserved.Legal|Privacy policy|Modern Slavery Act Transparency Statement|Sitemap|About US| Contact US: help@patsnap.com