Parallel robot
A robot and parallel technology, applied in manipulators, program-controlled manipulators, manufacturing tools, etc., can solve problems such as poor stiffness and complex structure, and achieve the effect of reducing weight and improving overall stiffness.
- Summary
- Abstract
- Description
- Claims
- Application Information
AI Technical Summary
Problems solved by technology
Method used
Image
Examples
Embodiment Construction
[0033] In order to make the object, technical solution and advantages of the present invention clearer, the implementation manner of the present invention will be further described in detail below in conjunction with the accompanying drawings.
[0034] An embodiment of the present invention provides a parallel robot, see figure 1 , the parallel robot includes a static platform 1, a dynamic platform 2 matching the static platform 1, and three kinematic branch chains installed in parallel between the static platform 1 and the dynamic platform 2.
[0035] Specifically, the static platform 1 is provided with a first driving device 11 , a second driving device 12 and a third driving device 13 . Wherein, the first driving device 11 , the second driving device 12 , and the third driving device 13 are installed on the static platform 1 at an angle of 120° to each other. The angles between the two of them are the same, which can make the force on the static platform 1 more uniform, im...
PUM
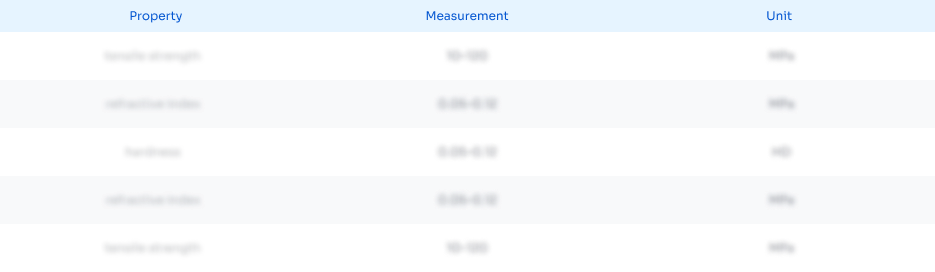
Abstract
Description
Claims
Application Information

- R&D Engineer
- R&D Manager
- IP Professional
- Industry Leading Data Capabilities
- Powerful AI technology
- Patent DNA Extraction
Browse by: Latest US Patents, China's latest patents, Technical Efficacy Thesaurus, Application Domain, Technology Topic, Popular Technical Reports.
© 2024 PatSnap. All rights reserved.Legal|Privacy policy|Modern Slavery Act Transparency Statement|Sitemap|About US| Contact US: help@patsnap.com