Cross column steel member assembling and welding process
A welding process and component technology, which is applied in the field of cross-column steel component assembly and welding process, can solve the problems of high labor intensity, low welding efficiency, and difficulty in guaranteeing welding quality, etc.
- Summary
- Abstract
- Description
- Claims
- Application Information
AI Technical Summary
Problems solved by technology
Method used
Image
Examples
Embodiment Construction
[0014] Such as figure 1 , figure 2 , image 3 As shown, a cross column steel component assembly and welding process of the present invention includes the following steps: a, the first web lath 1, the second web lath 2, and the third web lath 3 are assembled into a cross shape, wherein The first web lath 1 and the third web lath 3 have the same width, and are half of the width of the second web lath 2, the first web lath 1, the second web lath 2, the second web lath After the three web strips 3 are set up, the cross-shaped weld seam welding groove can be formed; b, after the first web strip 1, the second web strip 2, and the third web strip 3 are assembled, the four A cross-shaped web is formed by welding the welding groove of the first welding seam. The welding groove of each welding seam is made by submerged arc welding, and then the reverse side is carbon planed to clean the root, and then the submerged arc welding is used to fill the cover surface. The cross-shaped weldi...
PUM
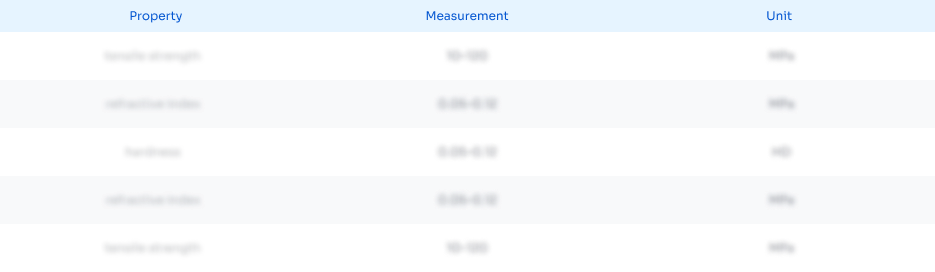
Abstract
Description
Claims
Application Information

- R&D
- Intellectual Property
- Life Sciences
- Materials
- Tech Scout
- Unparalleled Data Quality
- Higher Quality Content
- 60% Fewer Hallucinations
Browse by: Latest US Patents, China's latest patents, Technical Efficacy Thesaurus, Application Domain, Technology Topic, Popular Technical Reports.
© 2025 PatSnap. All rights reserved.Legal|Privacy policy|Modern Slavery Act Transparency Statement|Sitemap|About US| Contact US: help@patsnap.com