Cut lamina drying control method and cut lamina drying system based on feedforward and feedback of HT moisture compensation
A technology of drying control and shredded leaves, which is applied in the fields of tobacco preparation, tobacco, food science, etc., and can solve the problems of large adjustment of process parameters such as air temperature, unfavorable product internal quality, and influence on control accuracy, etc.
- Summary
- Abstract
- Description
- Claims
- Application Information
AI Technical Summary
Problems solved by technology
Method used
Image
Examples
Embodiment Construction
[0030] The present invention will be further described below in conjunction with the accompanying drawings.
[0031] like figure 2 As shown, the control block diagram of the inventive control method is taken as an example of the drum drying process of a certain second-class brand cigarette formula shredded leaf A module in a factory:
[0032] Step 1: Install the first moisture meter and electronic flow scale at the outlet of the HT moisture regainer, and collect the leaf silk moisture at the outlet of the HT moisture regainer in real time X 1 and silk flow M 1 ;
[0033] Step 2: Calculate the silk moisture X at the outlet of the HT conditioner1 The first given value X of the silk moisture at the entrance of the drum of the silk dryer 01 The difference ΔX 1 , using the difference signal ΔX 1 As the input signal of the first pneumatic actuator, after the signal is converted into a current analog signal by digital-to-analog conversion, the first pneumatic actuator outputs t...
PUM
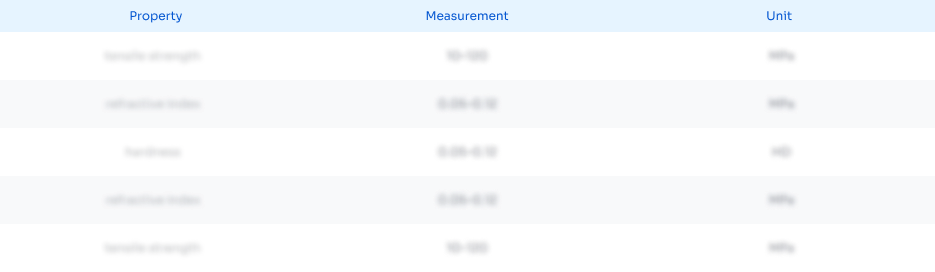
Abstract
Description
Claims
Application Information

- R&D
- Intellectual Property
- Life Sciences
- Materials
- Tech Scout
- Unparalleled Data Quality
- Higher Quality Content
- 60% Fewer Hallucinations
Browse by: Latest US Patents, China's latest patents, Technical Efficacy Thesaurus, Application Domain, Technology Topic, Popular Technical Reports.
© 2025 PatSnap. All rights reserved.Legal|Privacy policy|Modern Slavery Act Transparency Statement|Sitemap|About US| Contact US: help@patsnap.com