Lead hydrometallurgical technology through utilizing lead sulfate
A technology of lead sulfate and zinc hydrometallurgy, applied in the direction of improving process efficiency, etc., can solve problems such as not realizing large-scale production
- Summary
- Abstract
- Description
- Claims
- Application Information
AI Technical Summary
Problems solved by technology
Method used
Image
Examples
example 1
[0075] Example 1: Leaching
[0076] An enterprise volatilized zinc oxide in a kiln, and leached lead sulfate slag after recovering zinc and indium. The slag contains 21.89% lead, all of which are lead sulfate, containing 3.5% Zn and 10.2% S.
[0077] The leaching solution is a chloride salt solution, NaCl 280g / L, Ca 2+ 13g / L. Leaching conditions: Add 500g (dry weight) of slag to 5L of leaching solution, leaching under stirring conditions, liquid-solid ratio 10:1, temperature 80°C, leaching time 1.5 hours, leaching end point pH 4.5.
[0078] The leach residue contains 0.9% Pb, the leach residue rate is 96%, and the leach solution contains Pb 21.1 g / L.
example 2
[0079] Example 2: Leaching
[0080] A company leached lead and silver slag with high acid, containing Pb 15.54% (dry basis), sampled 588g, added 5L containing Ca 2+ 14g / L, NaCl 260g / L leaching solution, stirring and leaching at 80°C for 1.5 hours, the filtered and dried leaching residue weighed 451g, containing 1.36% Pb. The leaching solution + washing water totaled 5.32L, containing 16.0g / L Pb, and the Pb leaching rate was 93.15% %.
example 3
[0081] Example 3: Leaching
[0082] Lead paste leaching of waste lead-acid batteries: In the battery recycling workshop of a lead smelter, the dismantled lead sludge contains 76.04% lead (dry basis). Take 100g of lead paste, 2L of leachate, and the ingredients of the leachate are NaCl 320g / L, HCl 20g / L, the leaching temperature is 85°C, the leaching time is 2 hours, the pH of the leaching end point is 2.0, and Ca(OH) is added 2 Adjust the pH to 4.5. After filtration, the filtrate + washing water is 2.1L, containing 34.8g / L of Pb, and the lead leaching rate is 96%.
PUM
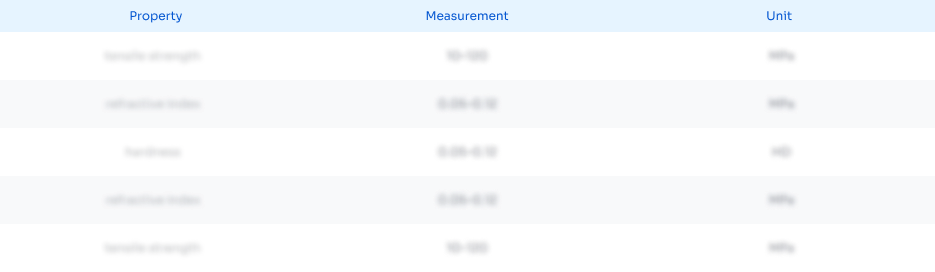
Abstract
Description
Claims
Application Information

- R&D
- Intellectual Property
- Life Sciences
- Materials
- Tech Scout
- Unparalleled Data Quality
- Higher Quality Content
- 60% Fewer Hallucinations
Browse by: Latest US Patents, China's latest patents, Technical Efficacy Thesaurus, Application Domain, Technology Topic, Popular Technical Reports.
© 2025 PatSnap. All rights reserved.Legal|Privacy policy|Modern Slavery Act Transparency Statement|Sitemap|About US| Contact US: help@patsnap.com