Vertical/short take-off and landing flying wing layout aircraft
An aircraft and layout technology, applied in the field of flying wing aircraft, can solve problems such as long take-off and landing roll distance, limited application, and requirements for enhancing pilot level
- Summary
- Abstract
- Description
- Claims
- Application Information
AI Technical Summary
Problems solved by technology
Method used
Image
Examples
Embodiment Construction
[0012] figure 1 The shown flying-wing layout aircraft according to an embodiment of the present invention includes a fuselage (1) and wings (2) integrated into one body, which has excellent aerodynamic performance. Ailerons (3) are positioned at the outer section of the wing (2) and are used for roll control during level flight. The elevator (5) is located at the rearmost part of the fuselage (1) and is used for pitch control in level flight. The twin vertical tails (4) are located behind the fuselage (1), and are used to enhance the heading stability in level flight, without any active rudder surfaces. The sleeve (8) traverses the fuselage (1), and is fixedly connected with the pods (23) of the two propellers (7) located on both sides of the fuselage (1) and in front of the wing (2). The power tilting of the front hair is realized by the rotation of the sleeve (8). When flying horizontally, the disc of the front propeller (7) is vertical, such as figure 2 The state of th...
PUM
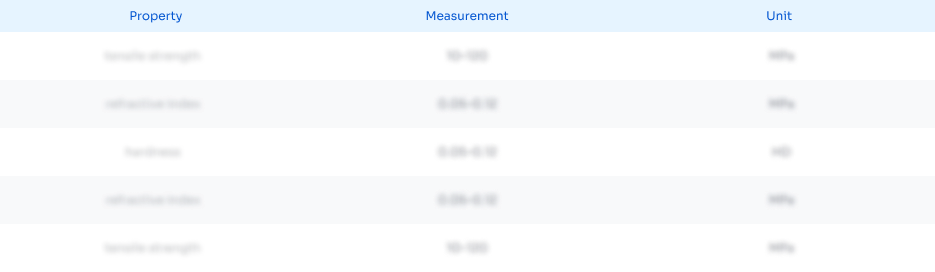
Abstract
Description
Claims
Application Information

- R&D
- Intellectual Property
- Life Sciences
- Materials
- Tech Scout
- Unparalleled Data Quality
- Higher Quality Content
- 60% Fewer Hallucinations
Browse by: Latest US Patents, China's latest patents, Technical Efficacy Thesaurus, Application Domain, Technology Topic, Popular Technical Reports.
© 2025 PatSnap. All rights reserved.Legal|Privacy policy|Modern Slavery Act Transparency Statement|Sitemap|About US| Contact US: help@patsnap.com