Polymer oil layer protective agent for drilling fluid and preparation method
A technology for oil layer protection and polymers, which is applied in the field of preparation of polymer oil layer protective agents for oilfield drilling fluids, can solve the problems of poor plugging effect of polymeric alcohols, great impact on drilling fluid performance, and inelastic deformability, etc., to achieve Enhanced plugging ability, mild and controllable preparation conditions, and improved temperature and salt resistance
- Summary
- Abstract
- Description
- Claims
- Application Information
AI Technical Summary
Problems solved by technology
Method used
Examples
Embodiment 1
[0023] Preparation method of the present invention is carried out as follows:
[0024] (1) Preparation of raw materials: Calculated based on the amount added per 80 ml of water: 95 ml of styrene, 5 ml of butyl acrylate, 40 ml of 2-acrylamido-2-methylpropanesulfonic acid, and 0.01 g of ammonium persulfate;
[0025] (2) Preparation of mother liquor: Add styrene, butyl acrylate, and 2-acrylamido-2-methylpropanesulfonic acid into water according to the ratio of raw materials in step (1), and mix well to form a primary mother liquor;
[0026] (3) Mother liquor emulsification: Add 5 grams of any type of allyl ether sulfonate (such as allyl ether sodium sulfonate) to the mother liquor obtained in step (2) to obtain a mixed solution A, A solution The mass concentration is 6%;
[0027] (4) Polymerization reaction: first pass nitrogen gas into the mixed solution in step (3) for 25 minutes, then heat to 70°C, add ammonium persulfate according to the raw material ratio in step (1), and t...
Embodiment 2
[0032] Preparation method of the present invention is carried out as follows:
[0033] (1) Preparation of raw materials: Calculated based on the amount added per 120 ml of water: 85 ml of styrene, 65 ml of butyl acrylate, 5 ml of 2-acrylamido-2-methylpropanesulfonic acid, and 0.2 g of ammonium persulfate;
[0034] (2) Preparation of mother liquor: Add styrene, butyl acrylate, and 2-acrylamido-2-methylpropanesulfonic acid into water according to the ratio of raw materials in step (1), and mix well to form a primary mother liquor;
[0035] (3) Mother liquor emulsification: Add 5 grams of any type of allyl ether sulfonate (such as allyl ether sodium sulfonate) to the mother liquor obtained in step (2) to obtain a mixed solution A, A solution The mass concentration is 20%;
[0036] (4) Polymerization reaction: first pass nitrogen gas into the mixed liquid in step (3) for 35 minutes, then heat to 70°C, add ammonium persulfate according to the raw material ratio in step (1), and th...
Embodiment 3
[0041] Preparation method of the present invention is carried out as follows:
[0042] (1) Preparation of raw materials: Calculated based on the amount added per 100 ml of water: 90 ml of styrene, 50 ml of butyl acrylate, 25 ml of 2-acrylamido-2-methylpropanesulfonic acid, and 0.1 g of ammonium persulfate;
[0043] (2) Preparation of mother liquor: Add styrene, butyl acrylate, and 2-acrylamido-2-methylpropanesulfonic acid into water according to the ratio of raw materials in step (1), and mix well to form a primary mother liquor;
[0044] (3) Mother liquor emulsification: Add 5 grams of any type of allyl ether sulfonate (such as allyl ether sodium sulfonate) to the mother liquor obtained in step (2) to obtain a mixed solution A, A solution The mass concentration is 35%;
[0045] (4) Polymerization reaction: first pass nitrogen gas into the mixed liquid in step (3) for 30 minutes, then heat to 70°C, add ammonium persulfate according to the raw material ratio in step (1), and t...
PUM
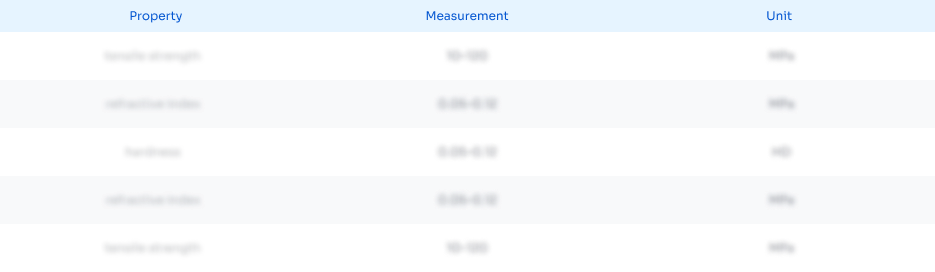
Abstract
Description
Claims
Application Information

- R&D
- Intellectual Property
- Life Sciences
- Materials
- Tech Scout
- Unparalleled Data Quality
- Higher Quality Content
- 60% Fewer Hallucinations
Browse by: Latest US Patents, China's latest patents, Technical Efficacy Thesaurus, Application Domain, Technology Topic, Popular Technical Reports.
© 2025 PatSnap. All rights reserved.Legal|Privacy policy|Modern Slavery Act Transparency Statement|Sitemap|About US| Contact US: help@patsnap.com